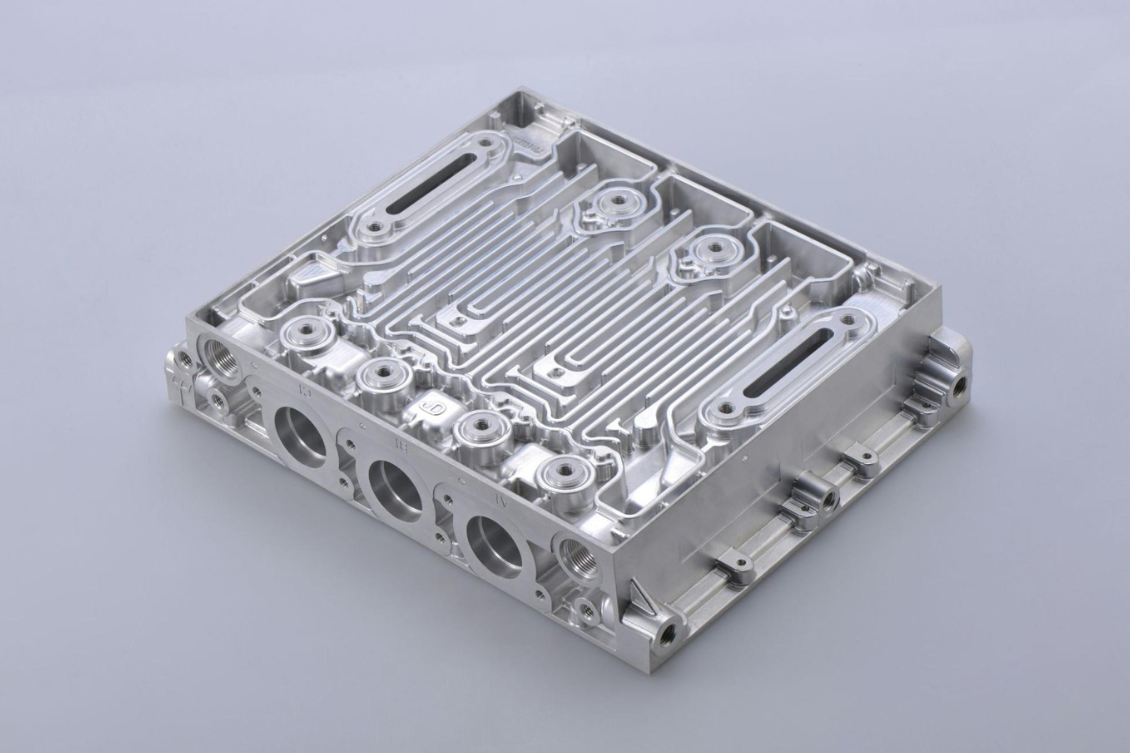
Non-recurring engineering (NRE) costs are critical, one-time expenses incurred during the design, development, and testing of a new product before mass production begins. These costs cover the essential activities needed to transform a concept into a market-ready product, including initial design work, prototype development, and production setup. NRE costs play a pivotal role in the production process by ensuring that all necessary groundwork is laid efficiently and effectively, minimizing risks, and paving the way for a smoother and more cost-effective transition to full-scale manufacturing. Properly managing NRE costs is essential for maintaining budget control and achieving timely product launches.
Initial Product Design and Engineering
Initial Product Design and Engineering is the starting stage in the lifecycle of any new product. It encompasses the creative and technical processes that transform a concept into a tangible design ready for development. At this crucial juncture, the focus is on translating ideas and requirements into detailed specifications that will guide the entire product development journey.
The process begins with comprehensive research and ideation, where designers and engineers collaborate closely to understand market needs, user preferences, and technological feasibility. This phase is not just about generating ideas but also about evaluating them rigorously to ensure they align with business goals and customer expectations. Clear communication and alignment among stakeholders—designers, engineers, and product managers—are vital to laying a solid groundwork that minimizes the risk of costly revisions later on.
Once a concept is selected, the design phase kicks into high gear. Here, CAD (Computer-Aided Design) tools are instrumental in creating detailed digital models that visualize every aspect of the product—from its dimensions and materials to its functional components and assembly processes. Iterative prototyping and testing play a crucial role during this phase, allowing for adjustments and refinements based on real-world feedback and technical constraints.
Moreover, during Initial Product Design and Engineering, it’s essential to consider manufacturability and scalability. Design choices made early on can have significant implications for production costs and timelines. Therefore, engineers work closely with manufacturers to optimize designs for efficiency and ease of assembly, ensuring that the transition from prototype to mass production is seamless.
In essence, the Initial Product Design and Engineering phase is about laying a robust foundation for the entire product development journey. By investing time and resources upfront to clarify requirements, validate concepts, and optimize designs, companies can mitigate risks associated with NRE costs. This proactive approach not only enhances product quality and market readiness but also contributes to long-term cost savings and competitive advantage in the marketplace.
Prototyping and Testing
The prototyping and testing phase begins with creating and testing prototypes, which are crucial for evaluating the design, functionality, and manufacturability of a product. These prototypes provide valuable insights and help identify potential issues early in the process. Testing these prototypes under various conditions ensures that the product meets the desired standards and performs as expected.
Based on the test results, iterative redesigns are made to refine and improve the product. This cycle of testing and redesigning continues until the product meets all specifications and requirements. Iterative redesigns help optimize the product and address any issues before mass production.
The final step is the validation and verification processes. Validation ensures that the product fulfills its intended use and meets user needs, while verification checks that the product complies with all design specifications and regulatory standards. These processes involve rigorous testing and quality assurance checks, which are essential for ensuring that the product is ready for mass production without any unforeseen issues.
Tooling and Equipment
The tooling and equipment phase involves the creation of custom molds and dies, which are essential for mass production. These tools are designed to produce precise and consistent parts, ensuring high-quality output. Custom molds and dies are a significant investment, but they are crucial for maintaining the efficiency and accuracy of the manufacturing process.
In addition to molds and dies, special machinery and equipment setups are necessary to support the production line. This includes machinery tailored to specific production needs, such as CNC machines, injection molding machines, or stamping presses. Setting up this equipment involves careful planning and calibration to ensure optimal performance and minimal downtime.
The final step in this phase is the configuration of the assembly line and integration of automation tools. Assembly line configuration involves arranging equipment and workstations to facilitate a smooth and efficient production flow. Automation tools, such as robotic arms and automated guided vehicles (AGVs), are integrated to enhance productivity and reduce labor costs. By automating repetitive tasks, companies can achieve higher precision and consistency in their manufacturing processes.
Together, these investments in tooling and equipment are essential for establishing a robust and efficient production line, ultimately ensuring the successful mass production of the product.
Regulatory Approvals
Regulatory approvals are pivotal for ensuring products meet legal and safety standards. This process begins early with identifying requirements, formulating compliance strategies, and compiling technical documentation for submission.
Compliance testing validates safety, performance, and environmental impact. Tests cover areas such as electrical safety, mechanical hazards, and resilience to environmental factors. Strict adherence to testing protocols and meticulous documentation are critical throughout this phase.
Documentation and training play essential roles in supporting regulatory submissions and facilitating product assembly and use. They include detailed technical specifications, comprehensive user manuals, safety data sheets, and educational materials for effective product deployment and maintenance.
Conclusion
In conclusion, navigating NRE costs requires a strategic approach across various stages of product development. From initial design and engineering to regulatory approvals, compliance testing, and documentation, each phase plays a crucial role in minimizing risks and maximizing efficiency.
By investing in thorough initial product design and engineering, companies set a strong foundation for success. Clear communication and collaboration between designers, engineers, and stakeholders ensure that products not only meet but exceed market expectations. This proactive approach not only reduces the likelihood of costly revisions but also accelerates time-to-market, enhancing competitiveness in dynamic industries.
Furthermore, achieving regulatory approvals and conducting comprehensive compliance testing are non-negotiable steps to ensure product safety and market readiness. Rigorous adherence to standards and meticulous documentation are key to navigating regulatory landscapes efficiently.
Ultimately, by prioritizing quality, innovation, and regulatory compliance from the outset, companies can mitigate NRE costs effectively. This not only safeguards investments but also fosters long-term growth and customer trust in an increasingly competitive marketplace.
Interested in OpenBOM? Reach out.
By: Jared Haw
Join our newsletter to receive a weekly portion of news, articles, and tips about OpenBOM and our community.