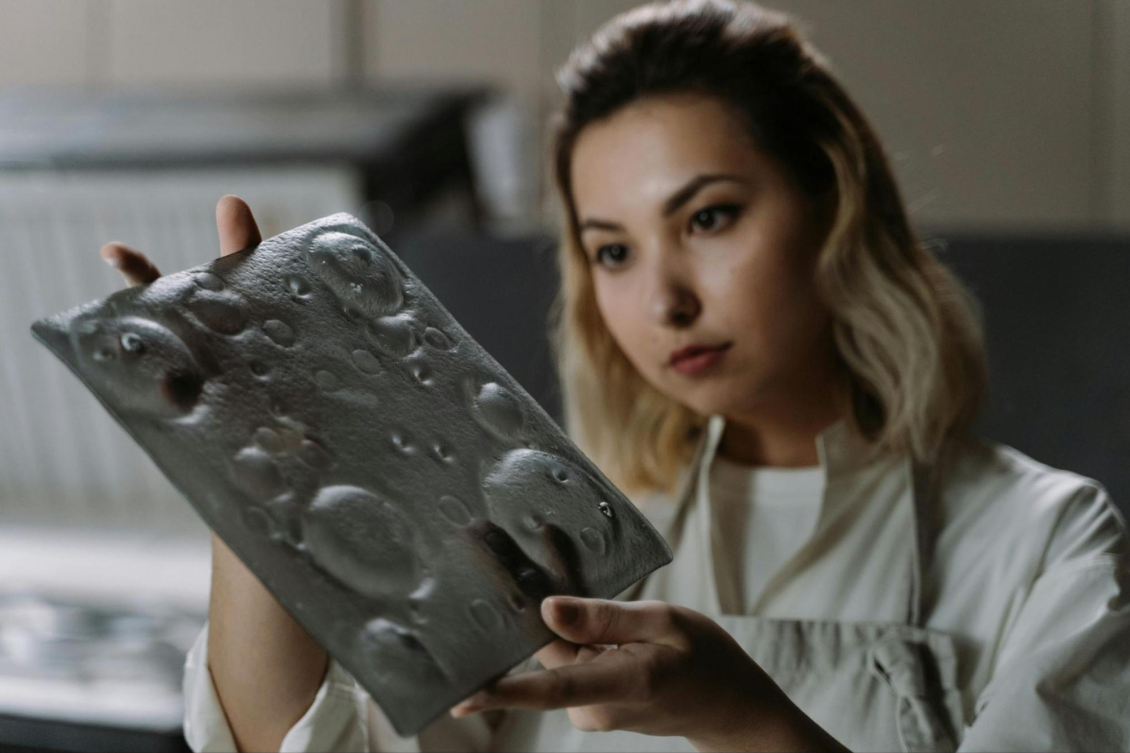
In the world of manufacturing and production, ensuring the quality and consistency of parts and products is paramount. One of the critical steps in achieving this is the First Article Inspection. This process serves as a validation method, conducted before a full-scale production run, to verify that a manufactured part or assembly meets all specified requirements and quality standards.
First Article Inspections act as a safeguard against potential errors, defects, and inconsistencies that can occur during production. By thoroughly inspecting the initial samples, manufacturers can identify and address any discrepancies early in the process, saving time, reducing costs, and maintaining customer trust.
This blog will delve into what First Article Inspections are, why they are crucial to manufacturing processes, and the risks associated with neglecting or improperly conducting these inspections. Understanding the importance of FAI can help manufacturers improve quality control, enhance compliance, and avoid costly mistakes.
What is a First Article Inspection?
A First Article Inspection is a comprehensive and systematic process of verifying that the first batch of parts in a production run conforms to all specified requirements. Essentially, it is an initial check conducted before moving to full-scale production, ensuring that the manufacturing process can reliably produce parts that meet design specifications and quality standards.
The First Article Inspection process involves a detailed examination and measurement of a sample part from the first production run against the original engineering drawings, specifications, and any other relevant documentation. This inspection is not merely a visual check but includes dimensional measurements, material verification, and functional testing, depending on the product’s complexity and criticality. The goal is to confirm that the production process is set up correctly and that all equipment, tooling, and procedures are adequate to produce parts consistently within the required tolerances.
First Article Inspections are widely used in industries where precision and quality are non-negotiable, such as aerospace, automotive, defense, medical devices, and electronics. In these sectors, even minor deviations from the specified standards can lead to severe consequences, including safety risks, product recalls, and significant financial losses. For this reason, companies in these industries often follow stringent protocols to ensure the integrity of their products.
The Importance of First Article Inspections
First Article Inspections play a crucial role in ensuring the quality, reliability, and consistency of manufactured parts and assemblies. By verifying that the initial production run meets all specified requirements, First Article Inspections help manufacturers avoid potential issues that could arise during full-scale production. Here’s why First Article Inspections are so important:
1. Ensures Conformance to Design and Quality Standards:
First Article Inspections is a critical step in confirming that a part or assembly produced matches the original design specifications and quality standards. By inspecting and measuring a sample from the first production run, manufacturers can identify any discrepancies or deviations from the design before they become larger issues in mass production. This proactive approach ensures that every subsequent part produced will meet customer expectations and regulatory requirements.
2. Prevents Costly Errors and Rework
Detecting and correcting errors early in the manufacturing process can save significant time and money. If a problem is identified during a First Article Inspection, it can be addressed immediately, before full production is underway. This minimizes the risk of large quantities of non-conforming parts being produced, which would otherwise lead to costly rework, scrap, or even recalls. By investing time and resources upfront in the First Article Inspection, manufacturers can reduce the overall cost of quality.
3. Provides Evidence for Compliance and Traceability
For industries that are highly regulated, such as aerospace, automotive, and medical devices, having documented evidence of compliance is critical. First Article Inspection provides a formal record that the parts and processes meet all necessary requirements. This documentation is invaluable for traceability, quality audits, and demonstrating compliance with industry standards and customer contracts.
4. Mitigates Risks of Production Delays
By catching potential issues at the start, First Article Inspections can prevent delays that would occur if defects or non-conformities were discovered later in the process. Addressing problems early means that the production line can run smoothly without interruptions caused by unexpected quality concerns, ensuring that products are delivered on time.
Key Elements of the First Article Inspection Process
The First Article Inspection process is a thorough and structured approach to validating the quality and compliance of the first parts produced in a manufacturing run. To ensure that the inspection is comprehensive and effective, several key elements need to be addressed. These elements form the foundation of The First Article Inspection and help ensure that all aspects of the part or assembly conform to the specified requirements.
1. Review of Drawings and Specifications
The first step in the First Article Inspection process is to review all relevant engineering drawings, design specifications, and quality standards. This includes examining dimensional tolerances, material requirements, surface finishes, and any other critical features outlined in the documentation. A detailed understanding of these specifications is essential to perform an accurate and thorough inspection.
2. Selection and Preparation of the First Article Sample
A representative sample, known as the “first article,” is selected from the initial production run or pilot run. This sample should be produced using the same equipment, processes, materials, and settings intended for full-scale production. Preparing this sample involves ensuring it is free from any contamination or handling damage that could affect the inspection results.
3. Detailed Inspection and Measurement of All Features
The core of the process involves inspecting and measuring all features of the first article against the specified requirements. This includes verifying dimensions, tolerances, and geometric features using precision measurement tools like calipers, micrometers, coordinate measuring machines, and other specialized equipment. Material verification, hardness testing, and functional testing may also be performed to ensure compliance with design criteria.
4. Documentation and Reporting of Results
Every step and result of this process is documented in a First Article Inspection Report. This report serves as a formal record of the inspection findings and includes details such as measurement data, non-conformances, and corrective actions taken if necessary. The report is typically shared with both the supplier and the customer to provide transparency and evidence of compliance.
5. Identification and Addressing of Non-Conformities
If any deviations or non-conformities are discovered during First Article Inspections, they are identified and documented in the report. The next step involves analyzing the root causes of these non-conformities and implementing corrective actions to prevent recurrence. This step is crucial in ensuring that the production process is capable of consistently producing parts that meet all requirements.
6. Approval and Sign-Off by Relevant Stakeholders
Once The First Article Inspection is completed and any necessary corrective actions have been taken, the results are reviewed by relevant stakeholders, including quality assurance teams, engineering, and the customer (if required). Approval and sign-off on the report indicate that the first article meets all specifications and that the production process is ready for full-scale manufacturing.
Conclusion
The First Article Inspection is an essential part of the manufacturing process, serving as a critical checkpoint to ensure that the initial production run meets all design and quality standards. By thoroughly inspecting the first article, manufacturers can identify and address potential issues early, preventing costly errors, rework, and production delays. This not only helps maintain high-quality standards but also strengthens relationships with customers by providing documented evidence of compliance and quality assurance.
The First Article Inspection process is especially vital in industries where precision, safety, and regulatory compliance are paramount, such as aerospace, automotive, and medical devices. Skipping or improperly conducting First Article Inspections can lead to serious consequences, from production setbacks to financial losses and damaged reputations. Therefore, understanding the key elements of the process and adhering to best practices is crucial for any manufacturer committed to quality and continuous improvement.
By implementing effective First Article Inspections, manufacturers can reduce risks, optimize their processes, and ensure that they consistently deliver products that meet or exceed customer expectations. Whether you are a seasoned manufacturer or just starting to establish your quality control processes, investing in a robust strategy is a smart move toward building a reliable and efficient production system.
By: Jared Haw
Join our newsletter to receive a weekly portion of news, articles, and tips about OpenBOM and our community.