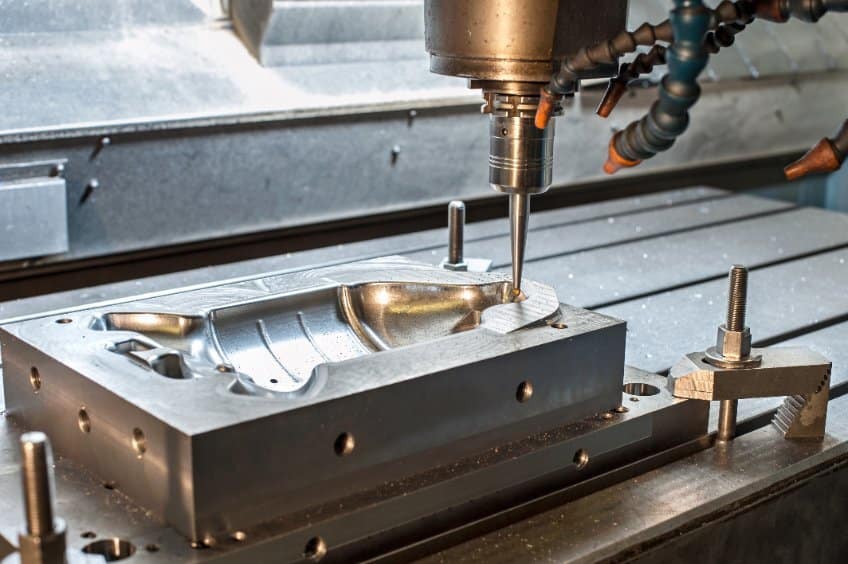
If you are developing a product, there will be a time when you need to transition from making prototypes to opening tooling so you can launch production. But, the question that’s asked is when do you transition from prototypes to opening up mass production tools?
What is Tooling?
Before we go on, let’s quickly go through what tools are and why they are needed. Mass production tools are an investment in equipment that allows you to replicate a part quickly, with high quality, and cost-effectiveness. If you did not have mass production tools then it would be impossible to reach economies of scale. Your output would be low, the product would be inconsistent, and you would be paying more for it.
The most common types of tools used in production are:
- Molds
- Dies
- Jigs & Fixtures
- Quality Tools
There are more but this will give you an idea of what tools are and their importance of them.
Tools also have a strong correlation with the final outcome of your product. Tools will affect your outcome in a number of ways, but here are the 3 common ways:
Pricing
Tooling affects the price of the part because of the output. To maximize the output you need to increase the number of cavities in the tool. For example, if there are two options. Option A has 2 cavities, and option B has 6 cavities then which option is cheaper? It will be option B. The cost of the tool will be more expensive for option B, but the cost per unit should be lower.
This is assuming that the size of the machine stays the same. If the size of your machine increases for option B then maybe the savings would be offset but the additional power needed to run a larger machine.
Quality
To be blunt, if the quality of your tool is not good then your part will not be good. The quality of your tool will affect tolerances, sink marks, part warpage, consistency, and more. The reason that your tool is yielding poor quality parts is that the tool might not be made with the correct materials, it’s out of tolerance, or it was poorly designed.
Investment
A large part of the investment for making a new product is tooling. If you look at most customized parts, you will need some sort of tool. This might be a plastic injection mold for your plastic parts that can range from $4,000 to $100,000/mold or a die-cut tool that might cost a few hundred dollars.
The most common tools you need for production are:
- Plastic Injection Molding Tools
- Liquid Silicone Rubber Injection Molds
- Die-Cast Tools
- Welding fixtures
- Assembling Jigs
These costs all add up.
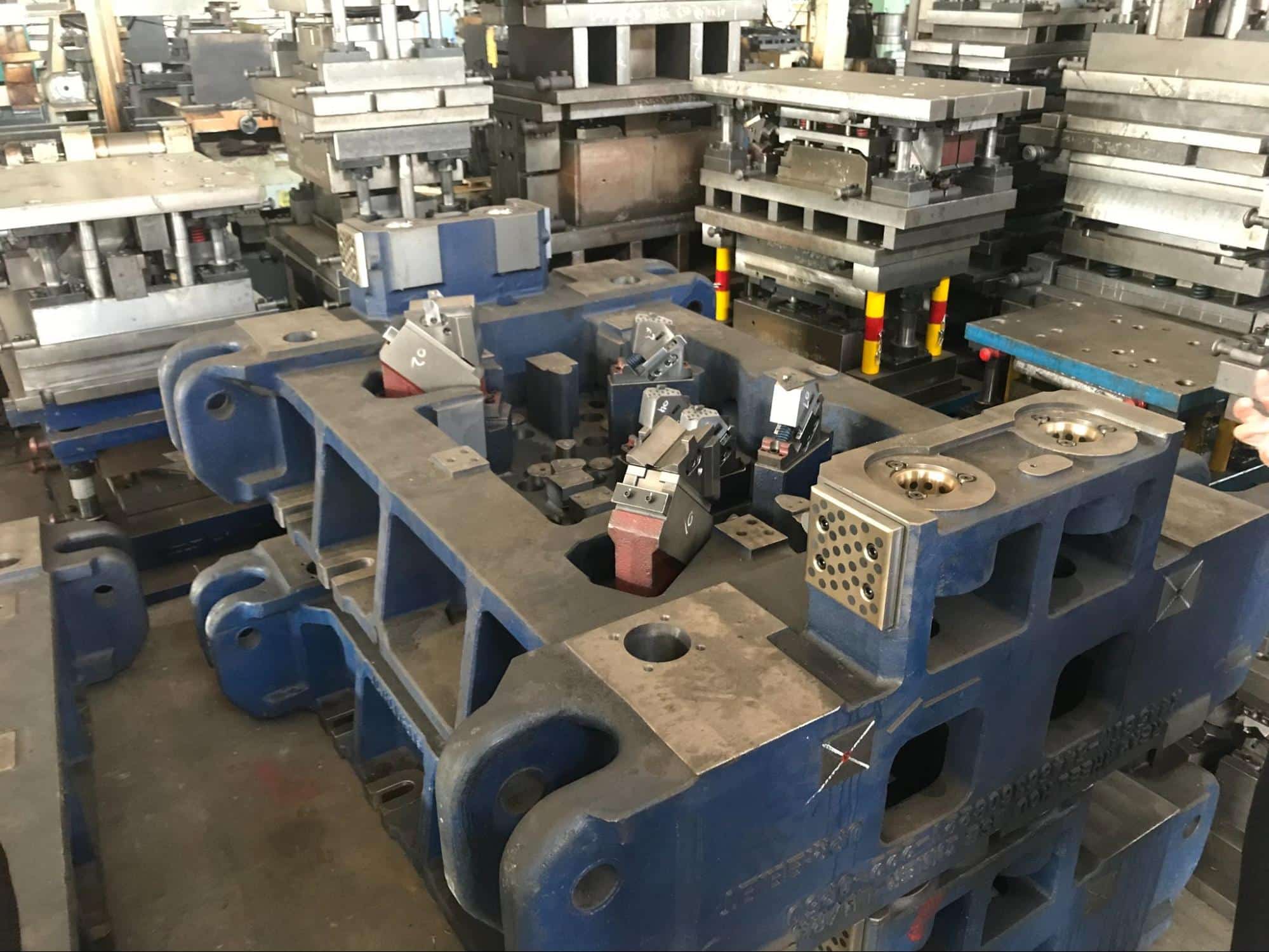
When to Open up Tools?
There is no doubt that tools are necessary for you to scale production. However, when do you open your tools? If you open tools too early, you might need to modify them and make them again which means you just doubled your tooling budget. On the other side, waiting too long means you delay your product launch, unable to proceed with some certification processes and more.
During the development phase, your contract manufacturer (CM) will most likely lead your design for manufacturing (DFM) process. During DFM, you will look at optimizing parts for production. This includes slightly re-designing a part for tooling.
The top common injection molding defects due to not properly designing your tools are:
- Sink marks
- Warping
- Flow lines
- Welding lines
The best time to open up tools is when the part, sub-assembly, and all parts that are dependent on it will not be changing. If there is anything that can directly or indirectly affect the part then you should not open the tool. When the part is ready, you can release it for tooling.
How can OpenBOM Help?
During the development project, there are many changes going back and forth between your team, contractors, and suppliers. Managing this data and making sure everyone is on the same page is difficult. If specific data is not properly passed from your team to the responsible parties, such as tool makers, then a lot of time and money will need to be spent in order to create the proper tools.
OpenBOM is a cloud-based PDM & PLM platform to manage your engineering and manufacturing data. Companies from startups to Fortune 500’s use OpenBOM to create a centralized database to bring in, store and manage their manufacturing data. With this infrastructure, users also use OpenBOM to streamline both their change management and PO processes.
If you need to improve the way you manage your data and processes, contact us today for a free consultation.
Regards,
Jared Haw
Join our newsletter to receive a weekly portion of news, articles, and tips about OpenBOM and our community.