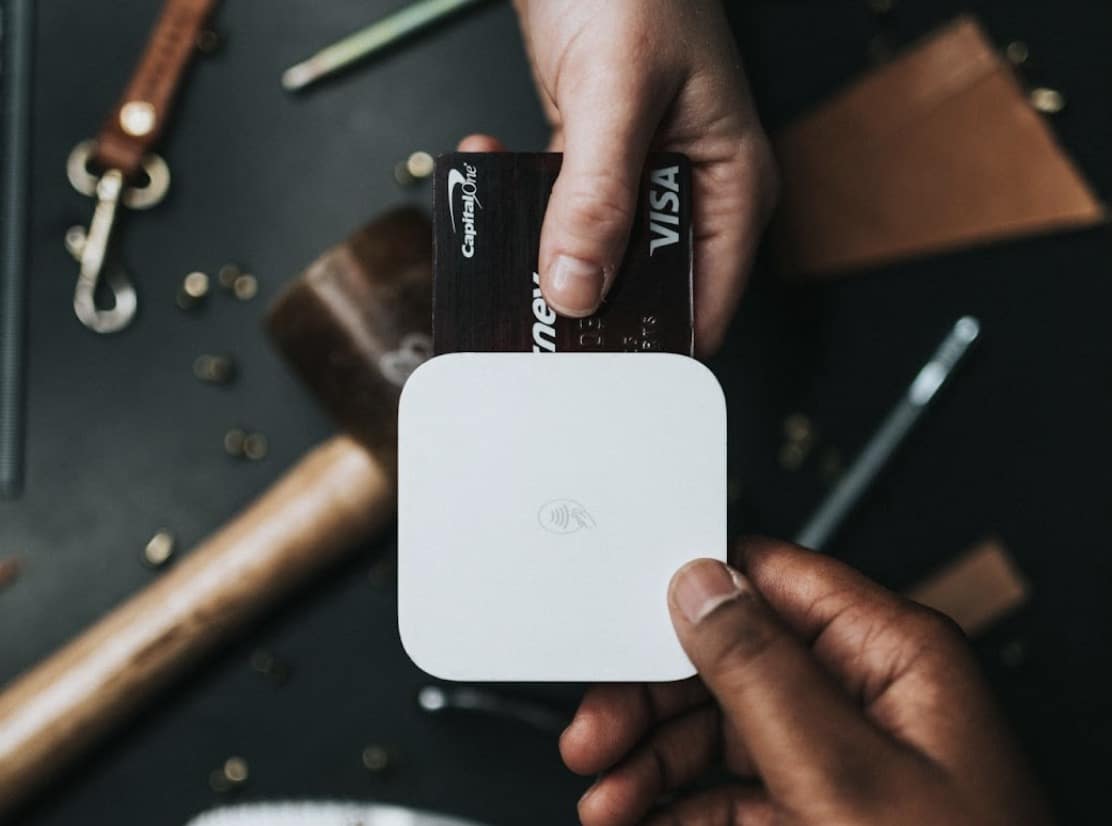
One of the main drivers of the costs of your product will be the production costs. This is also what we fight to decrease. Let’s see what production costs are and see how we calculate them.
What are Production Costs?
Production costs are all the costs associated with manufacturing your product. This consists of the materials, fabrication, labor, supplies, overhead, and more. We can narrow these down into direct and indirect costs.
Direct Costs
According to Investopedia, direct costs are “a price that can be directly tied to the production of specific goods or services.” You can also look at direct costs as anything that is directly adding value to the product. These are costs that are specifically for a particular product rather than the general facility.
The two most common examples are:
- Labor that is directly involved in the production
- Raw materials
We can dig a bit deeper. From the image below, you can see 6 different parts with a number of costs. Those costs are material, diecast, polishing, and powder coating costs. These all provide direct value to the part so they are looked at as direct costs.
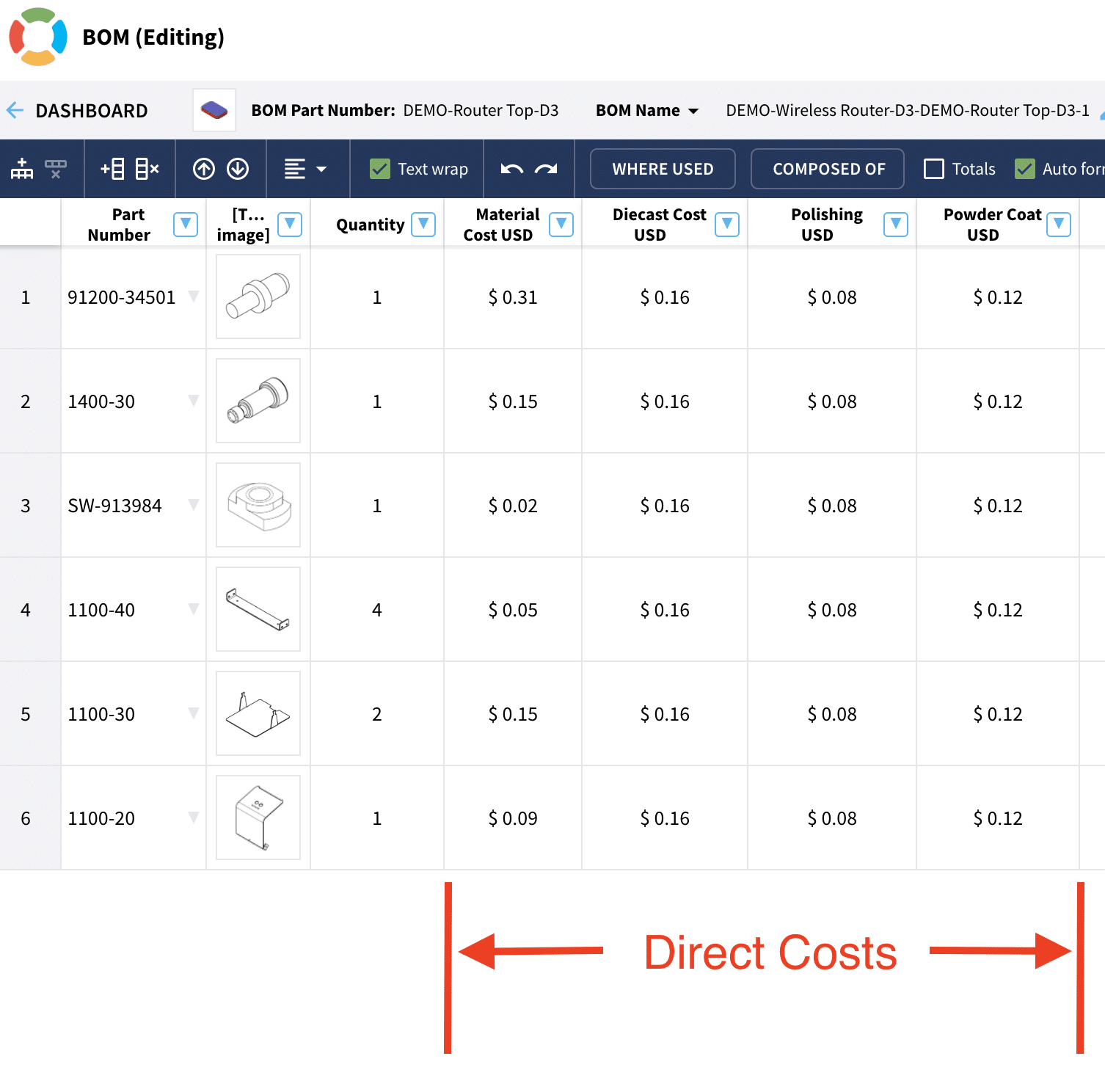
Indirect Costs
AccountingTools states that indirect costs “are production costs that cannot be directly associated with a produced unit.” Indirect costs usually have a larger scope because they entail everything that is not a direct cost.
You can further breakdown indirect costs into a few categories
Indirect Labor
Indirect labor are those who do not add direct value to the product. Direct labor would be the assemblers and operators that are fabricating and assembling the product. Indirect labor would be the employees not involved in the direct assembly. These include the engineering, supply chain, HR, finance, and other teams.
Manufacturing Overhead
Another type of indirect cost is manufacturing overhead. This consists of rent, utilities, water, and more.
Indirect Supplies:
This can be included in manufacturing overhead but I wanted to separate this type because of the overall scope. Indirect suppliers will include tools and equipment that are used to assemble and fabricate a product.
Taxes
The most common tax will be the VAT tax from Chinese suppliers. Depending on the industry and part, you might be able to receive some rebates. Talk to your supplier and see if they can share these rebates with you.
The picture shown here takes the previous example and adds a couple of different kinds of indirect costs, overhead, and taxes.
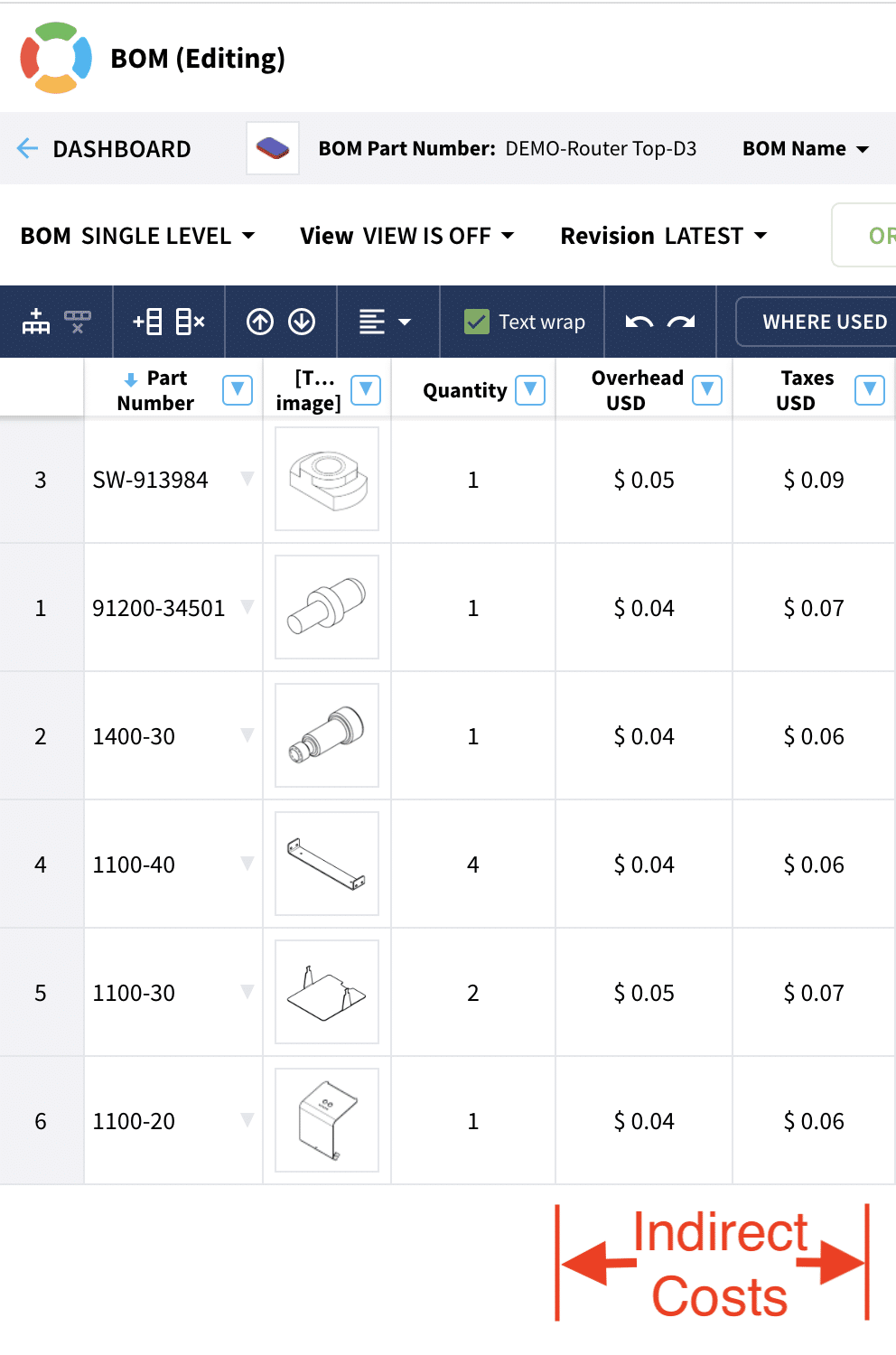
Total Production Costs
To figure out the production costs, you take the indirect costs + the direct costs. The picture below shows you the total costs by adding the indirect costs to direct costs.
Total Production Costs = Direct Costs + Indirect Costs
To apply this to our example, you will get the following:
Total Costs = Material Cost + Diecast Cost + Polishing Cost + Powder Coating + Overhead + Taxes
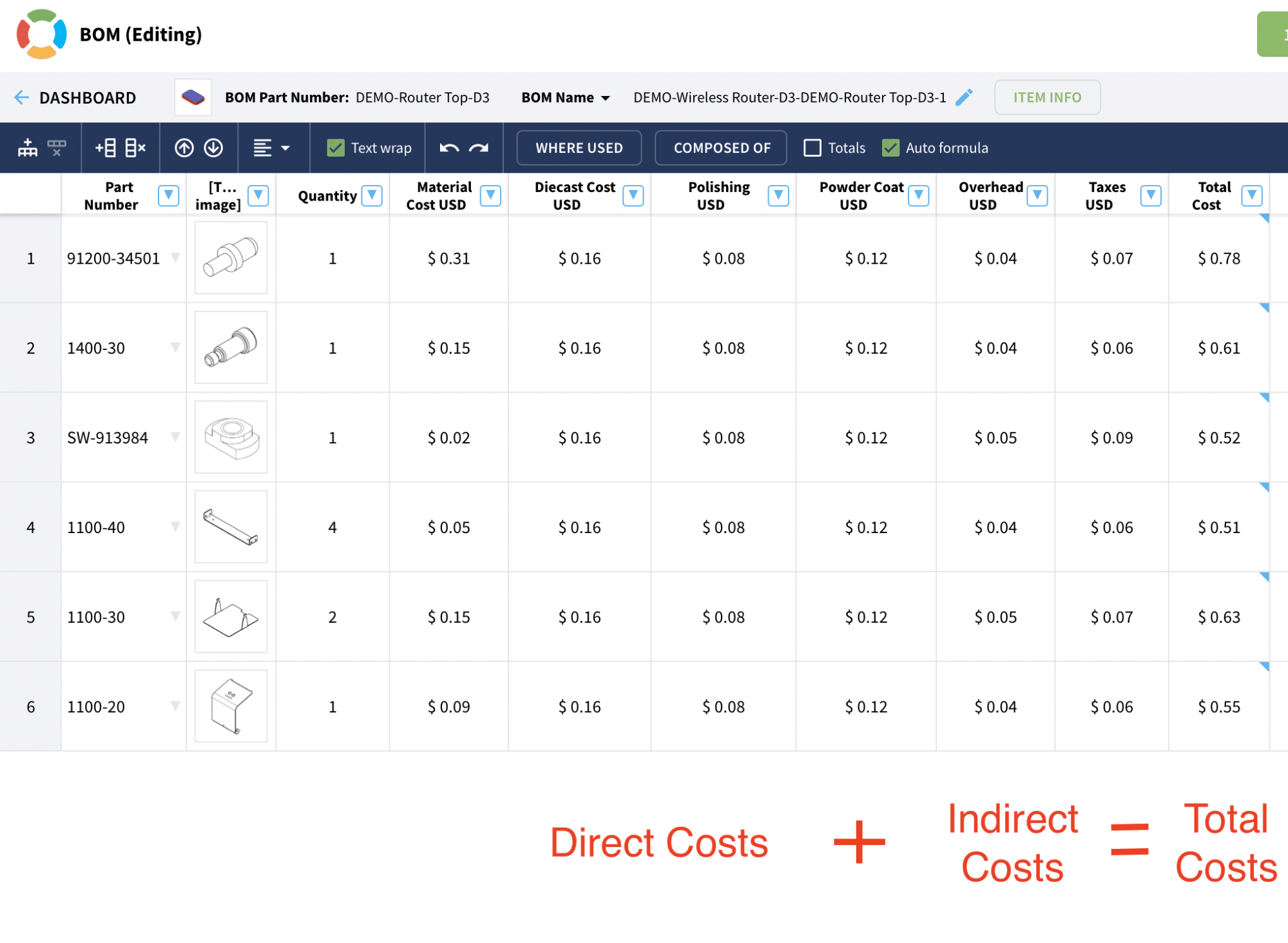
In the next blog, we will dive deeper and compare the differences between variable and fixed costs and how they affect the total cost.
How can we Help?
In the last couple of years, we’ve had part inflation and part shortages. As a result, manufacturing companies have been forced to source multiple alternative components while tracking the prices for all components. This has created managing your data in spreadsheets chaotic. The solution is OpenBOM.
OpenBOM is a cloud-based platform to manage your engineering and manufacturing data. Companies from startups to Fortune 500’s use OpenBOM to create a centralized database to bring in, store and manage their manufacturing data. With this infrastructure, users also use OpenBOM to streamline both their change management and PO processes.
If you need to improve the way you manage your data and processes, contact us today for a free consultation.
Regards,
Jared Haw
Join our newsletter to receive a weekly portion of news, articles, and tips about OpenBOM and our community.