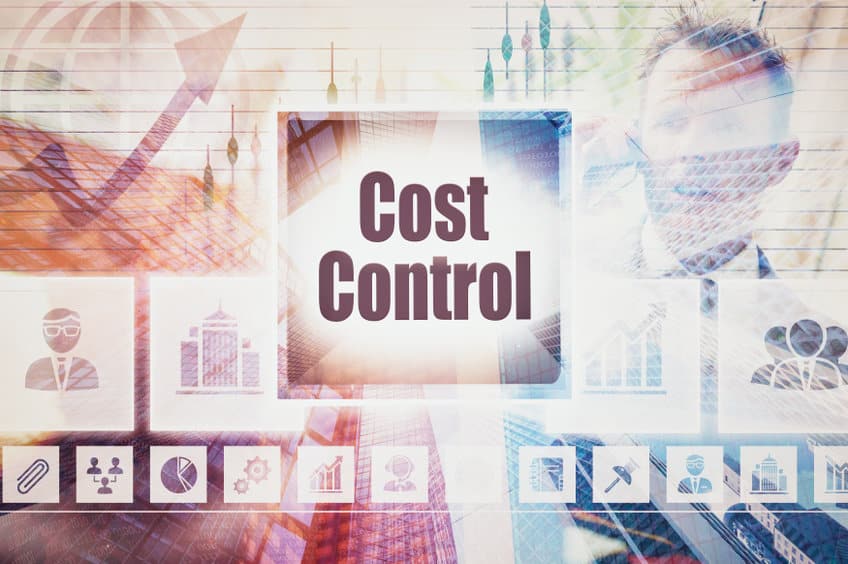
In our blog last week, What are Production Costs and how to Calculate them, we looked at the differences between direct and indirect costs. This post is going to dive a bit deeper into costs and compare the differences between variable and fixed costs and the effect these have on your production costs.
Fixed Costs
Investopedia defines fixed costs as ”any expenses that remain the same no matter how much a company produces.” That means whether you are at 25% or 75% capacity, these costs will remain the same.
Common examples of fixed costs:
- Rent/Mortgage
- Operational Employees (not related to labor)
- Tax (depends on location & structure)
- Depreciation
- Insurance
Variable Costs
Investopedia also defines variable costs as “any costs that a company incurs that are associated with the number of goods or services it produces.” Variable costs are tied together to the overall production costs because they fluctuate with the volume of production.
Therefore, you have a correlation between variable costs and the volume of the orders. If the volume of the orders goes up then the variable costs go down. If the volume of the orders goes down then the variable costs go up.
Two of the most common examples of variable costs:
- Labor
- Raw Materials
What Do Both these mean?
You most likely have heard someone in your company say we need to reach economies of scale. What this means is that you can achieve certain savings as production becomes more efficient. In layman’s terms, buy more products, and get a cheaper production price.
Essentially, economies of scale are when you are able to minimize both variable and fixed costs. To reach economies of scale, you also need sustainability within your production output. If you place one large order, you won’t achieve economics of scale. You will just receive a discount on variable costs but fixed costs will remain the same.
To achieve economies of scale, you can spread fixed costs throughout the cost of the unit. The higher the annual sales volume, the lower those fixed costs go.
Below is a quick example of how increasing the annual sales will decrease your fixed cost. The assumption here is that if you have $2 million in annual sales, both your rent and employees will not be at full capacity.
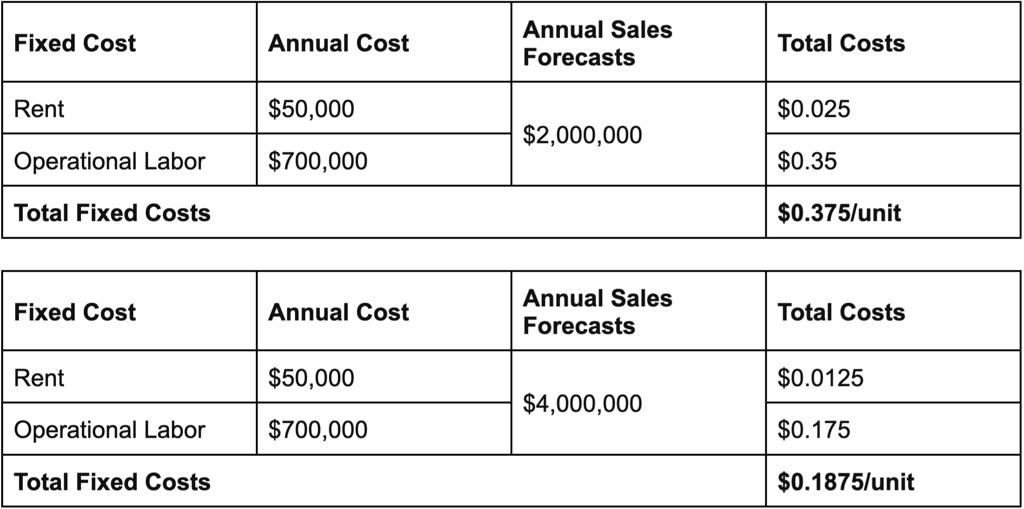
The key takeaway here is that moving towards full capacity and full efficiency within fixed costs will lead you to economies of scale which in turn provides you with a more favorable quote.
However, you also don’t want to make more products to only achieve economies of scale without having the demand. Making more products without sales will only increase our overall costs (i.e. inventory costs).
Variable costs on the other hand are a bit easier to decrease. It strictly comes down to the size of a particular order. The larger the order size, the greater discount you can receive on variable costs (i.e. raw material).
For example, we have a BOM for a product with costing for an order of 1,000 units. The second image shows the same BOM but with costing for an order of 15,000 units.
As you can see, the costs for each item, with the exception of overhead, are decreased as the volume goes up. The reason overhead does not go down is that for this single example overhead is looked at as a fixed cost.
As explained earlier, if we can sustain a higher level of production and the annual forecasts increase then overhead can decrease.
The percent of the tax paid remains the same at 13%. What this means is that an order of 15,000 units or 1,000 units has the same tax percentage, 13%. However, the dollar amount paid in tax per unit will decrease for 15,000 units because the overall cost is lower per unit.
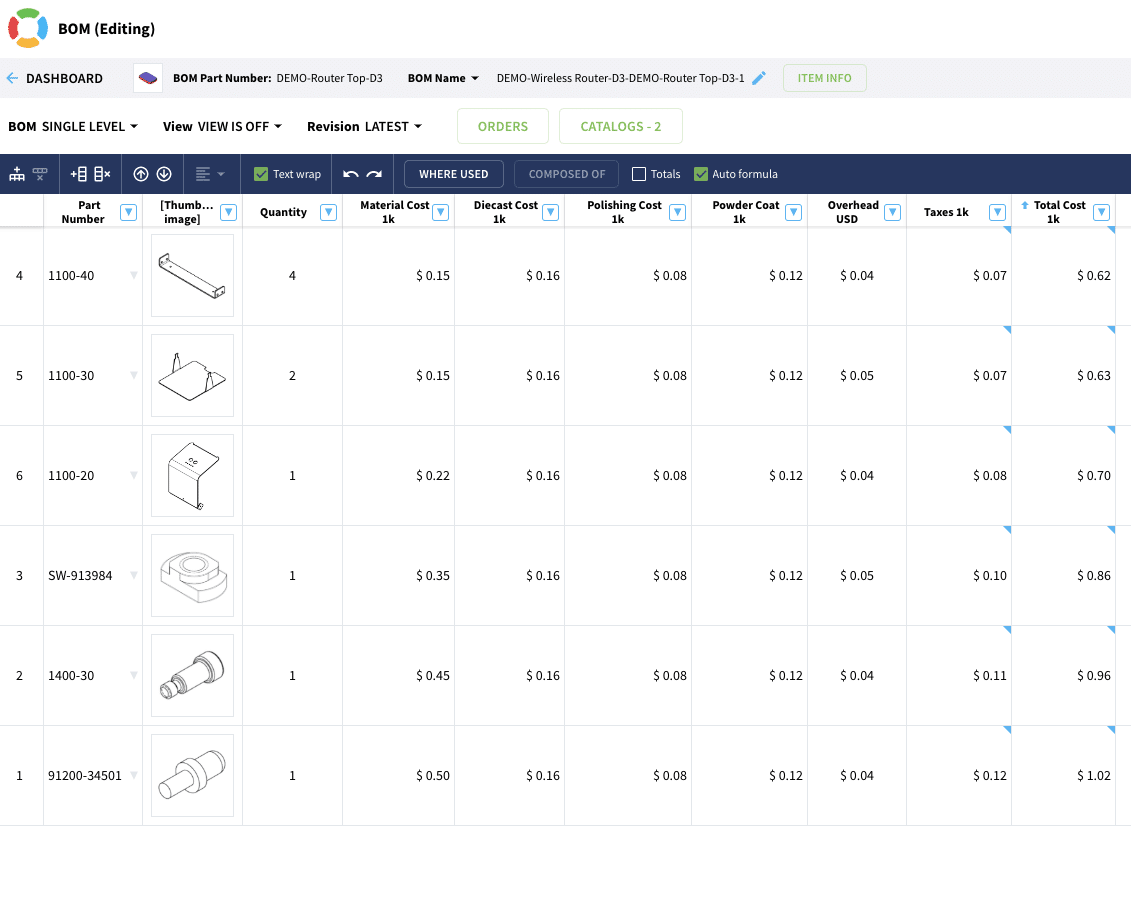
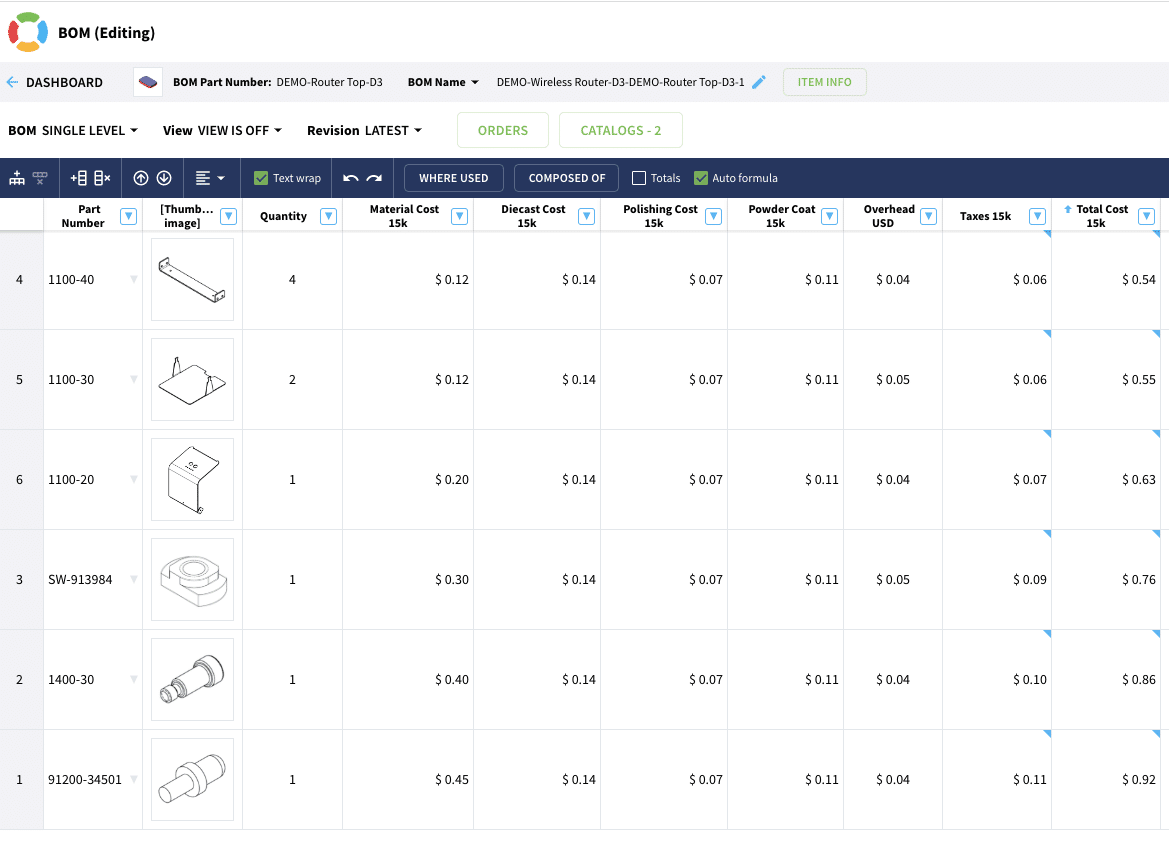
How can we Help?
In the last couple of years, we’ve had part inflation and part shortages. These all have an effect on the volume of the orders which affects both variable and fixed costs. As a result, manufacturing companies have been forced to source multiple alternative components while tracking the prices for all components. This has created managing your data in spreadsheets chaotic. The solution is OpenBOM.
OpenBOM is a cloud-based platform to manage your engineering and manufacturing data. Companies from startups to Fortune 500’s use OpenBOM to create a centralized database to bring in, store and manage their manufacturing data. With this infrastructure, users also use OpenBOM to streamline both their change management and PO processes.
If you need to improve the way you manage your data and processes, contact us today for a free consultation.
Regards,
Jared Haw
Join our newsletter to receive a weekly portion of news, articles, and tips about OpenBOM and our community.