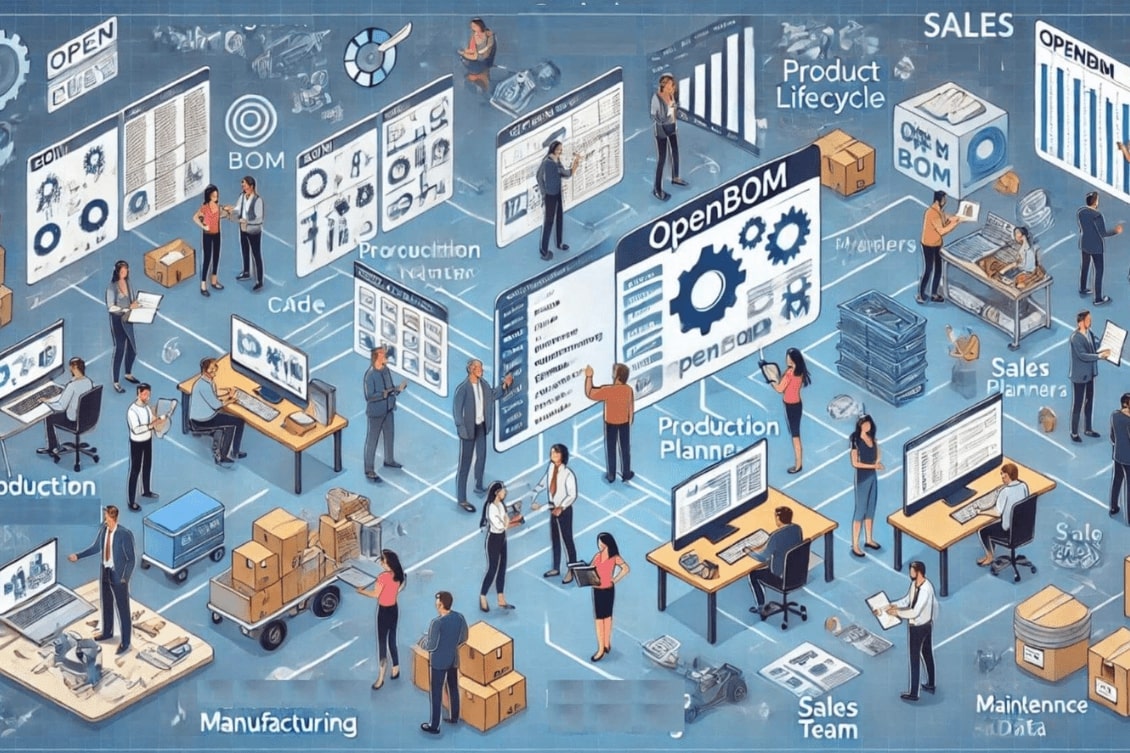
Product development success relies on the synergy between multiple team members. It is a teamwork. Engineers, project managers, procurement teams, production planners, sales, support, and maintenance personnel – all play important roles in bringing a product to life and an entire product lifecycle management. Each team member brings unique skills and responsibilities, but all share a common need: effective collaboration and access to accurate, real-time data. For years, PLM software has focused on how to support the entire product lifecycle and product data management. PLM solutions originally started from document management for CAD files and made multiple attempts to expand from core engineering data and engineering release processes to support a wide range of business processes in the organization – expanding to service lifecycle management, manufacturing BOM, bill of process and production process as well as supply chain management.
Unfortunately, after many years, traditional PLM is still focusing on the top of the iceberg – engineering data, engineering release, and change management. Here is the review provided by CIMdata Research.
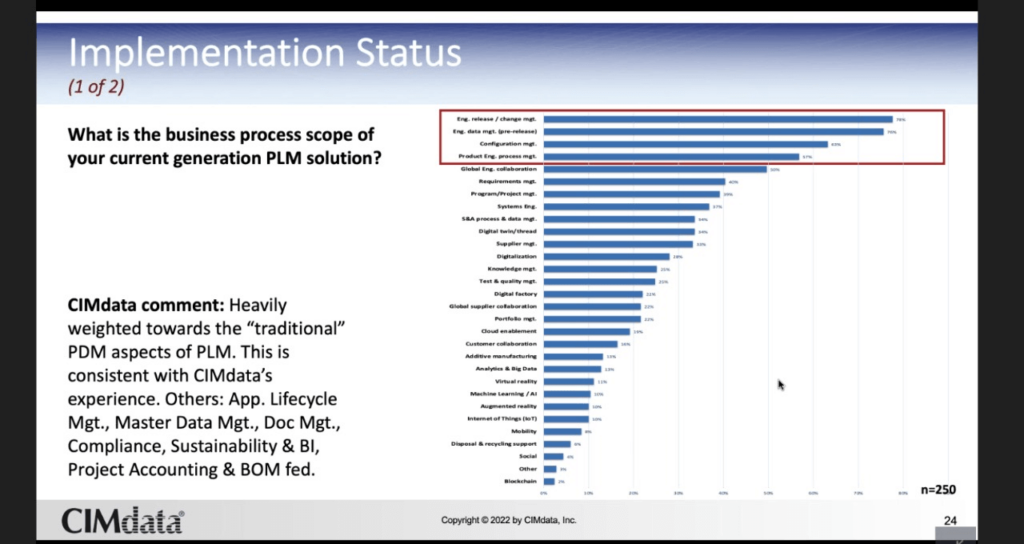
One of the main reasons for the limitations in the adoption of PLM software can be – the monolithic architecture (single database/tenant), complex user experience, and limited data management flexibility of legacy PLM systems.
That’s where OpenBOM steps in, providing a seamless and connected digital thread that revolutionizes product development. OpenBOM focuses on two fundamental improvements: (1) introducing new graph-based and flexible data management architecture
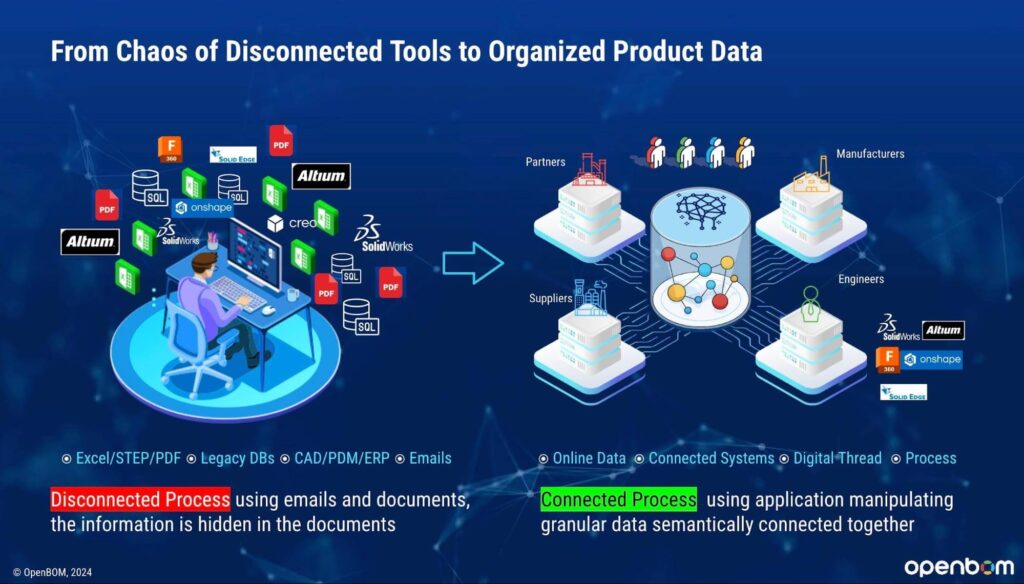
…and (2) collaboration process to support agile product development processes.
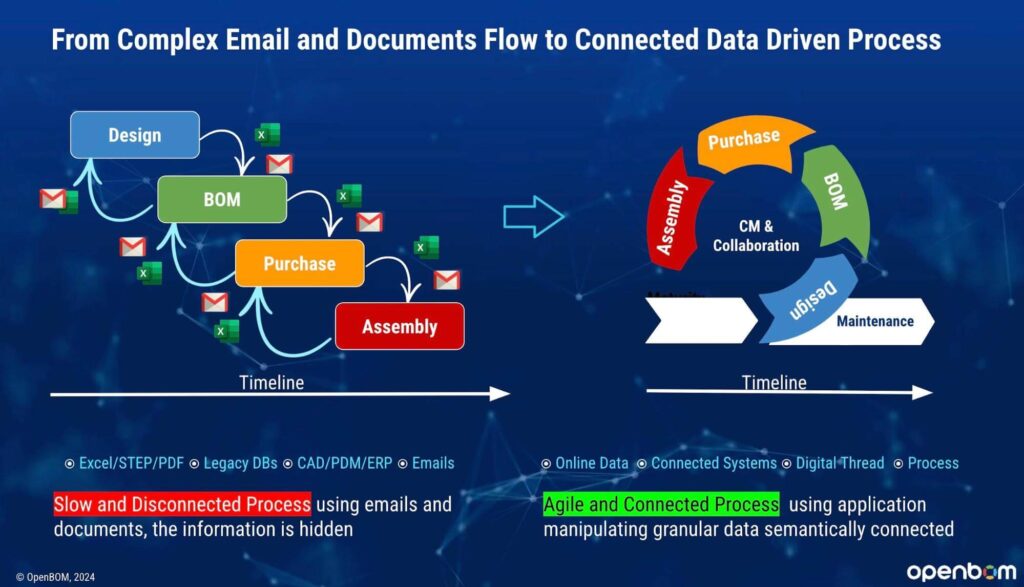
It is important to see how OpenBOM can empower each team member to do their best work and streamline the entire process. We identify 6 main “role-based” groups involved in the entire product lifecycle – (1) Engineers, (2) Management (product and project), (3) Procurement, (4) Manufacturing and production planning, (5) Sales, (6) Support and Maintenance. Let’s speak in a more detailed way about each of them and how they impact product lifecycle management (PLM) business strategy.
Engineers: Ensuring Design Precision and Flexibility Across Disciplines
Engineers are at the heart of product development, tasked with creating designs that meet technical specifications and production requirements. OpenBOM simplifies the engineering workflow by allowing engineers in various disciplines (mechanical, electrical, software, etc.) to access and update BOMs in real-time without version control issues. It integrates seamlessly with popular CAD tools, so engineers can stay in their familiar design environments while contributing to a shared BOM. With OpenBOM, they can easily create and manage engineering BOMs, capture changes, and communicate effectively with downstream teams—reducing rework and ensuring accuracy in the final product.
Project and Product Managers: Keeping Projects on Track and on Time
Project and product managers need to oversee the entire lifecycle of a product, from conception to completion. They rely on accurate data to make informed decisions, track progress, and adjust schedules. OpenBOM gives them visibility into the product structure, making it easy to track changes and dependencies in real-time. With OpenBOM’s xBOM capabilities combined with dashboards, visualization and reporting allow to managers to see the status of components, inventory levels, and production timelines, allowing them to manage risks proactively and keep projects on schedule. This level of insight supports better planning, resource allocation, and timely delivery of projects.
Procurement: Streamlining Vendor Coordination and Cost Management
Procurement teams are responsible for sourcing parts and managing relationships with suppliers. OpenBOM centralizes procurement data, manages vendors and suppliers, enabling procurement professionals to view updated BOMs, vendor information, and cost data in one place. This transparency makes it easier to order the correct parts, negotiate better prices, and avoid delays. By connecting procurement activities directly to the product data, OpenBOM helps procurement teams quickly respond to changes, manage alternate components, and reduce lead times, which is especially critical in today’s fast-paced supply chains.
Production Planners: Enabling Smooth Transition from Design to Manufacturing
Production planners need to ensure that the right parts are available at the right time to support manufacturing schedules. OpenBOM’s manufacturing BOM (MBOM) functionality helps them convert engineering BOMs into MBOMs that reflect production requirements. With OpenBOM, planners can visualize the product structure, plan for production runs, and collaborate with engineering on manufacturability issues. The system’s real-time updates prevent delays caused by missing parts or miscommunication, making it easier to align production schedules with project timelines.
Sales: Empowering Data-Driven Customer Interactions
Sales teams rely on up-to-date product information to effectively communicate with customers. OpenBOM gives sales teams visibility into the product configuration and its variations, allowing them to respond accurately to customer inquiries, estimate costs, and confirm lead times. Sales can use OpenBOM “Sales BOM” to access data on configurations, system configurations, and pricing, so they’re equipped to provide customers with reliable quotes and timelines. This transparency builds trust with customers and improves the overall sales experience.
Support and Maintenance: Enhancing Post-Sale Service and Reliability
For support and maintenance teams, having access to accurate product information is essential to resolving issues quickly. OpenBOM provides a connected view of each product’s lifecycle, including detailed Service and Serial Number BOMs, part replacements, and historical changes. This information enables support teams to identify issues faster, recommend appropriate parts or services, and keep products operational. With OpenBOM, maintenance and support teams have all the data they need to ensure a product’s reliability throughout its lifecycle.
Overall Process Optimization: The Value of a Connected Digital Thread
By connecting everyone in the product development process, OpenBOM eliminates the inefficiencies of managing multiple spreadsheets, isolated databases, and manual data sharing. OpenBOM’s digital thread approach ensures that every team member has access to the latest data, enabling seamless collaboration and quick response to changes.
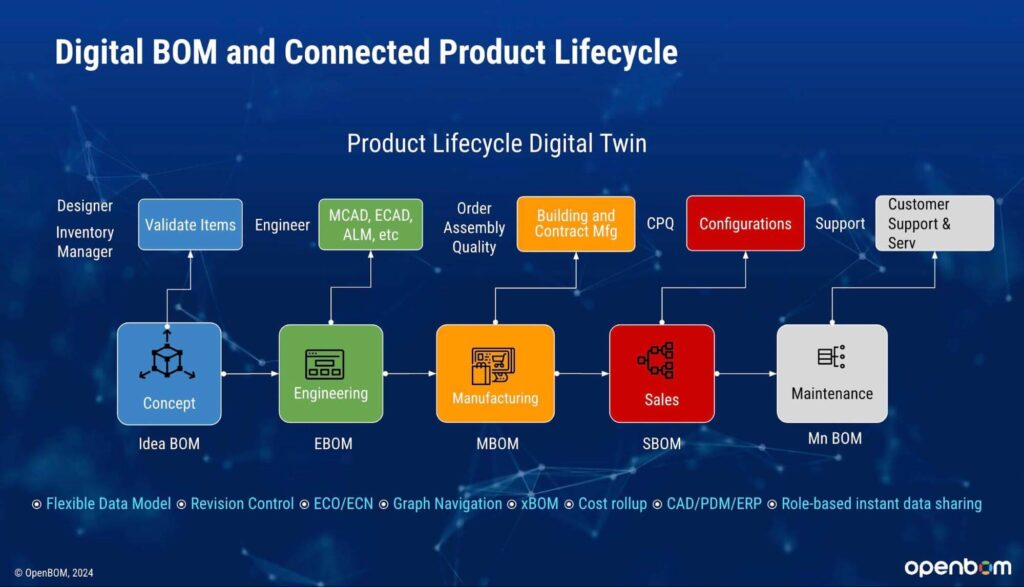
The shared, real-time multiple BOMs creates an entire product lifecycle digital twin and ensures that everyone is on the same page, reducing errors, saving time, and enhancing the overall efficiency of the product lifecycle.
Conclusion: A New Approach in Collaboration and Decision Process
OpenBOM brings each team member into a single, connected process, transforming how products are developed, manufactured, and maintained. Instead of spending time chasing down information or manually updating spreadsheets, checking emails and Dropbox for PDF files, team members can focus on adding value to the product and driving innovation.
The power of a connected, data-driven approach translates into faster time-to-market, lower costs, and a better customer experience. In today’s fast-paced and competitive environment, OpenBOM is the key to unlocking the potential of modern, collaborative product development.
REGISTER FOR FREE and check how OpenBOM can help you.
Best, Oleg
Join our newsletter to receive a weekly portion of news, articles, and tips about OpenBOM and our community.