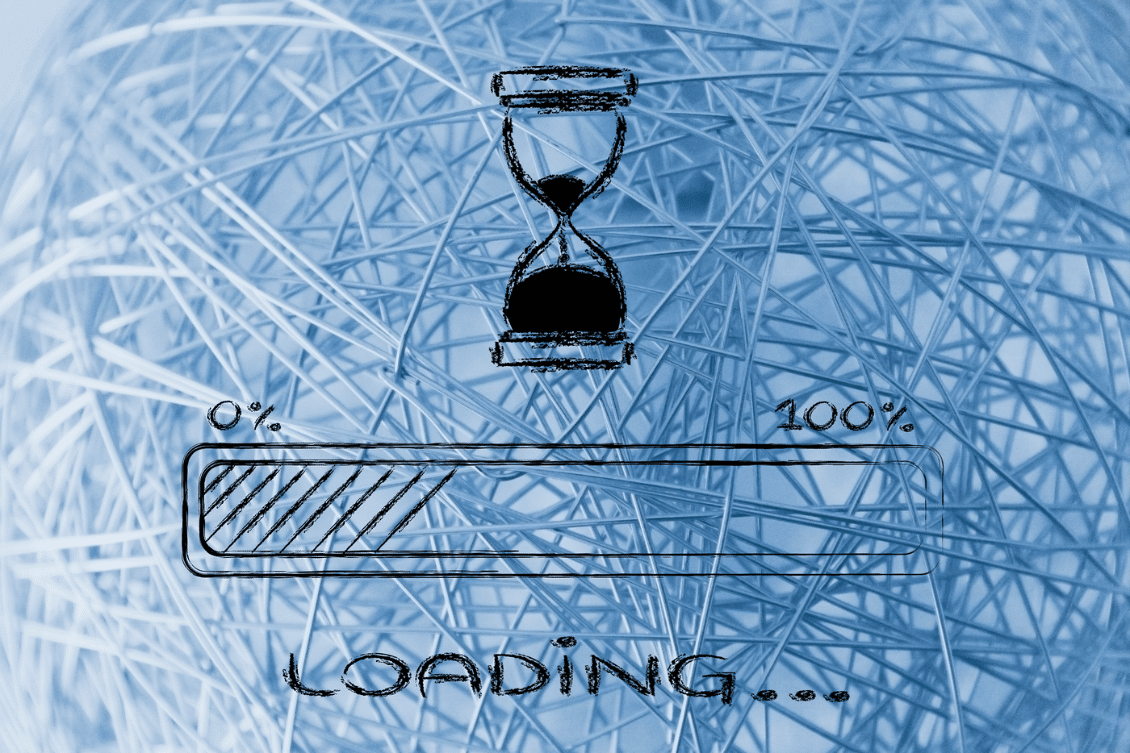
For the last few years, I’ve had the opportunity to chat with many engineers, business owners, executives, founders of hard-tech companies, and consultants searching for PLM solutions and implementing PLM solutions in different companies. One of the most fundamental questions I found the industry is struggling with is deciding when to implement PLM. Unfortunately, over the years, the PLM industry built a perception that PLM is only for large companies and when you are small and nimble, you don’t need it.
Old Habits Die Hard
There is something that needs to be said about years of bad practices and the experience of the engineers and companies to ‘patch’ their problems. The guilt can be split equally into two pieces – (1) engineers are not really interested in data management and processes. They need to figure out what they do and get annoying data management tasks off their lists. Therefore, a typical engineer working on design would be pretty ignorant when the question about data management and PLM comes up. (2) managers prefer not to manage engineering and product development processes and let them “figure it out”. This means that they allow processes to flow without many details, not focusing on roles or information flow.
Only after problems are starting to knock at their doors, do they start “paying attention”. When it happens, it is usually already very late. People are struggling to manage their product data, concerned that they are experiencing significant growth, and they were finding it tough to keep track of their product data and processes. Complex products, compliance requirements, and poor collaboration between teams – this is a typical picture of a “pre-PLM” environment.
After working with many customers, I think I can share more information about our experience and how to structure the adoption and learning process. Here are three steps I recommend that can help you to build a PLM playbook to introduce it in your company.
Product Lifecycle Management (PLM) is a system that helps businesses manage their product data, from design to end-of-life. PLM can improve collaboration, streamline processes, and increase efficiency, ultimately leading to cost savings and better products. But when is the right time to implement PLM?
Factors to Consider
The answer about starting PLM implementation is different for every company, but there are a few factors to consider when deciding if it’s the right time to implement PLM:
- Product Complexity: If your products are becoming more complex, it may be time to implement PLM. PLM can help manage the design and engineering process, keeping track of all changes, revisions, and approvals. You might not need a sophisticated system to manage assembly with 5 parts, but even so, I’d encourage you to keep reading.
- Growth: As companies grow, managing product data becomes more complex. If your business is experiencing growth, you may be handling more products, suppliers, and customers, making it challenging to keep track of product data. PLM can help manage this complexity and keep everything organized.
- Compliance Requirements: The number of regulatory requirements is growing and it can be very challenging to manage without a centralized system. PLM can help ensure that all products meet regulatory requirements and can provide a traceable audit trail. As a manager, this is your “ticket out of jail”.
- Collaboration: The teams are growing and manufacturing is a complex process that involves many people. If your company has multiple teams or departments involved in product development, collaboration can be a challenge. PLM can facilitate collaboration and communication between teams, streamlining processes and reducing errors.
- Customer Requirements: Customer-facing process. If your customers are requesting more transparency and access to product data, implementing PLM can help. With PLM, customers can access product information, specifications, and updates in real time.
Implementation Best Practices
Focus on Data
As soon as you decided you need a system to manage product lifecycle management, you should start thinking about the data (actually product and process data). Not focusing on how to get the right data, manage it, connect, and integrate it with other elements of your company environment can end up very badly. On to that, focus on how to bring data to the center of your decision-making process.
Build a Use Case – Design, Engineering, Procurement
The thread of a typical product lifecycle management and development circles around very fundamental processes – (1) how to manage design; (2) how to provide engineers to collaborate without limits; and (3) how to connect design and procurement in a single digital process. The fundamental engineering and manufacturing software is simple and requires a focus on important data.
Make Team and Management Alignment
It is extremely important to bring everyone on the same page. In traditional legacy PLM projects, it is called “management commitment or sponsorship”. What is more important and can severely impact anything you can (or cannot do) is to lay down the plan about how to bring the system to your team (or company) and start performing tasks (from #1).
Conclusion:
It is never late to start PLM implementation. It’s essential to consider the factors above and assess your current processes. If your company is experiencing growth, managing complex products, struggling with compliance, or seeking better collaboration, PLM may be the solution you need. With PLM, you can manage product data more efficiently, ultimately leading to cost savings and better products.
REGISTER FOR FREE and get access to OpenBOM’s 14-day trial program.
Best, Oleg
Join our newsletter to receive a weekly portion of news, articles, and tips about OpenBOM and our community.