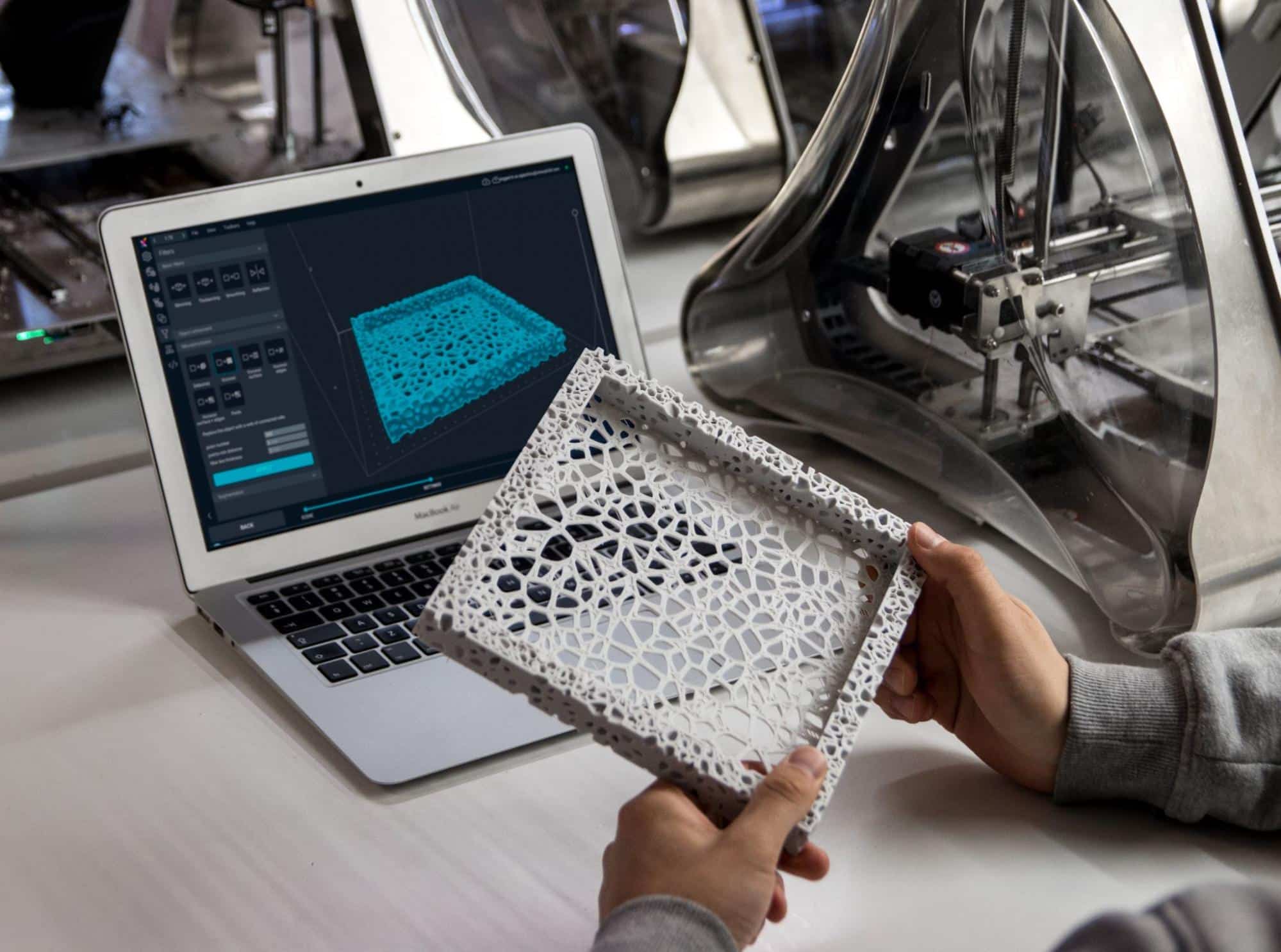
When you are preparing to launch your product, one important step is to transfer your product to your contract manufacturer (CM). This transfer of data is usually done at the request for quotation (RFQ) stage of the development process. The bill of materials (BOM) along with other data is provided to your CM so you can receive a quotation.
However, the accuracy and thoroughness of your data, such as your BOM, dictates the speed and accuracy of the quote you receive. For example, if you provide a BOM that is specified like the one in the image below then you can expect to receive a quote that’s not accurate or you will waste time with a lot of back and forth to confirm these specs.
The basic questions your supplier will ask will be:
- What kind of plastic?
- Which grade of stainless steel and aluminum?
- What is the Pantone color?
- What is a normal part finish?
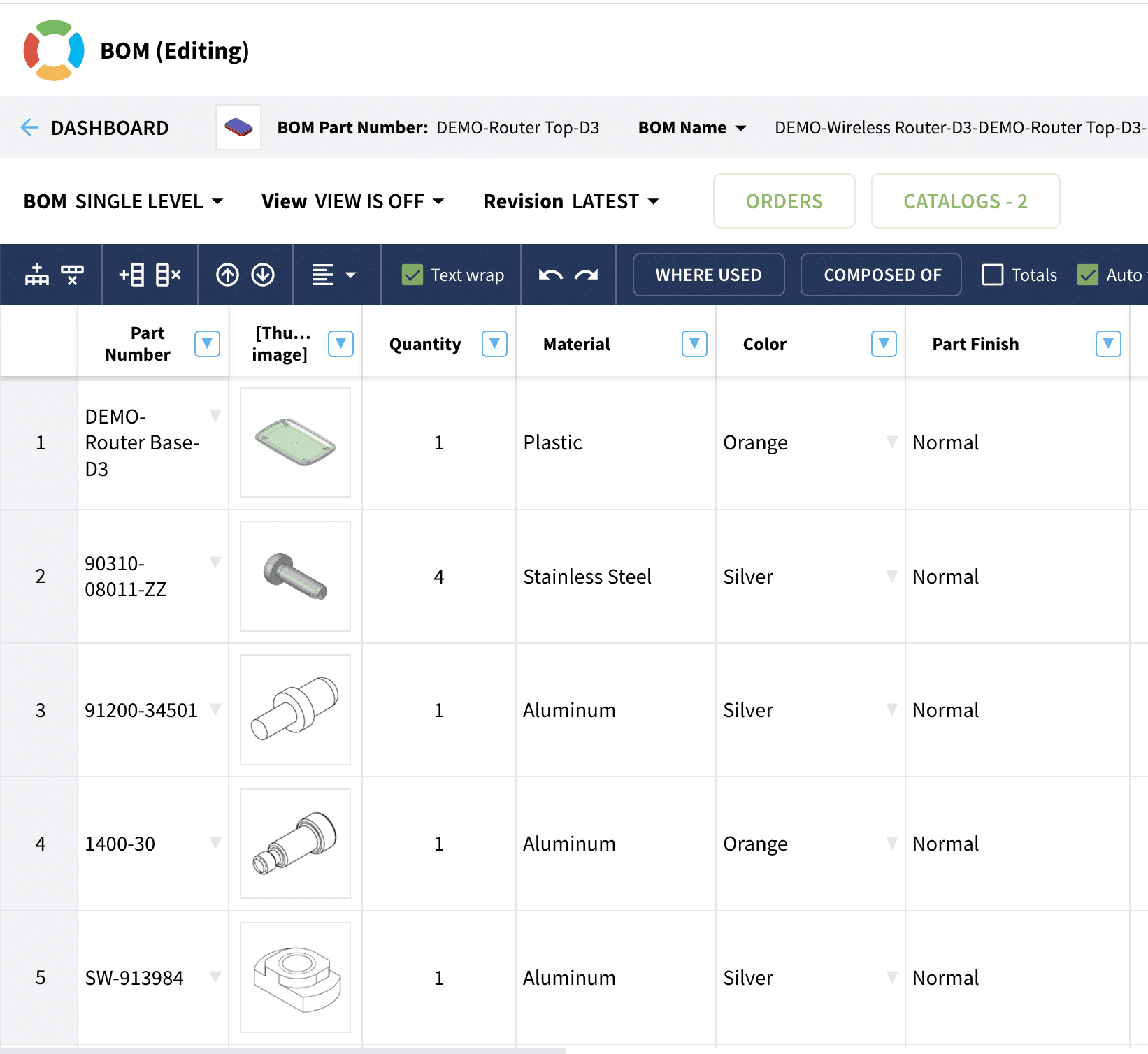
If you do provide a BOM that is not specified, like the one above, then you can expect the following:
Inaccurate Quotation or Prolonged Quotation
One of the purposes of the RFQ process is to receive quotes from multiple suppliers. If the BOM is not specified then you will receive either inaccurate quotes or a quote that seems to take forever.
The reason you will receive inaccurate quotes is simple. If the supplier does not know the material grade then they will make assumptions. The price for aluminum 6061 is different than aluminum 5052. The prices for ABS, POM, PC, and other plastics are also different. Lastly, the price of powder coat will be different than anodizing, electroplating, and more.
Not updating the BOM properly is another reason for incorrect quotes. If your quantities are wrong or if parts are not removed, this will result in your quotes being off and not truly knowing the price of your product.
If your CM receives a BOM that is not complete then they should work with you to specify these items. Specifying these items takes a lot of back and forth which feels a bit dragged out.
Incorrect Prototypes
If your supplier first creates a prototype and the BOM is not defined, you run the risk of receiving a prototype that is not acceptable. This will be because of functional and aesthetic issues.
The properties in aluminum 6061 and 5052 are different and might result in failures during testing. The same is for different types of plastics, stainless steel, and really any type of material.
While orange is a color, it is not how you define a color on the BOM. All colors have different shades and all those shades can be considered to be orange. For example, Pantone 1385 and Pantone 1645 are both orange. However, one is an amber-orange while the others is a melon-orange. Two completely different shades.
Having a prototype with either the incorrect color or the wrong material is a waste of a prototype and something that should never have occurred.
Prolonged Development
The risk of trying to develop a product with a BOM that is not defined is that you are working with incorrect assumptions. Working with incorrect assumptions will lead to multiple errors in the design. Multiple errors lead to prolonged development.
A common example of this will be during the design for manufacturing (DFM) stage. If your CM or another contractor supports you during DFM but your data is not updated or specified then expect a longer development cycle.
DFM is where you are able to transition your product from the prototype stage to something that can be made quickly and efficiently in production. If basic data points are missing then they will need to spend time defining everything.
Share BOM or Download a Package for CM
OpenBOM allows you to create a BOM from your favorite CAD system, automatically upload CAD files and generate derivatives in a neutral format (eg. PDF, STL, STEP, etc. ) and then either share or package your BOM, including all files into a zip file to be delivered to your CM. It will eliminate the mistakes and the need to manually create all information you need to share with CM. Check how easy you can do it in the following video.
What can you do today?
One overlooked part during the development process is updating and maintaining your BOM. There is a correlation between keeping a well-managed BOM and other product data with a successful product launch. Managing all of this in spreadsheets slows down the process and makes it difficult to collaborate. A centralized platform that connects your team, contractors, and suppliers is your solution.
OpenBOM is a cloud-based PDM & PLM platform to manage your engineering and manufacturing data. Companies from startups to Fortune 500’s use OpenBOM to create a centralized database to bring in, store and manage their manufacturing data. With this infrastructure, users also use OpenBOM to streamline both their change management and PO processes.
If you need to improve the way you manage your data and processes, contact us today for a free consultation.
Regards,
Jared Haw
Join our newsletter to receive a weekly portion of news, articles, and tips about OpenBOM and our community.