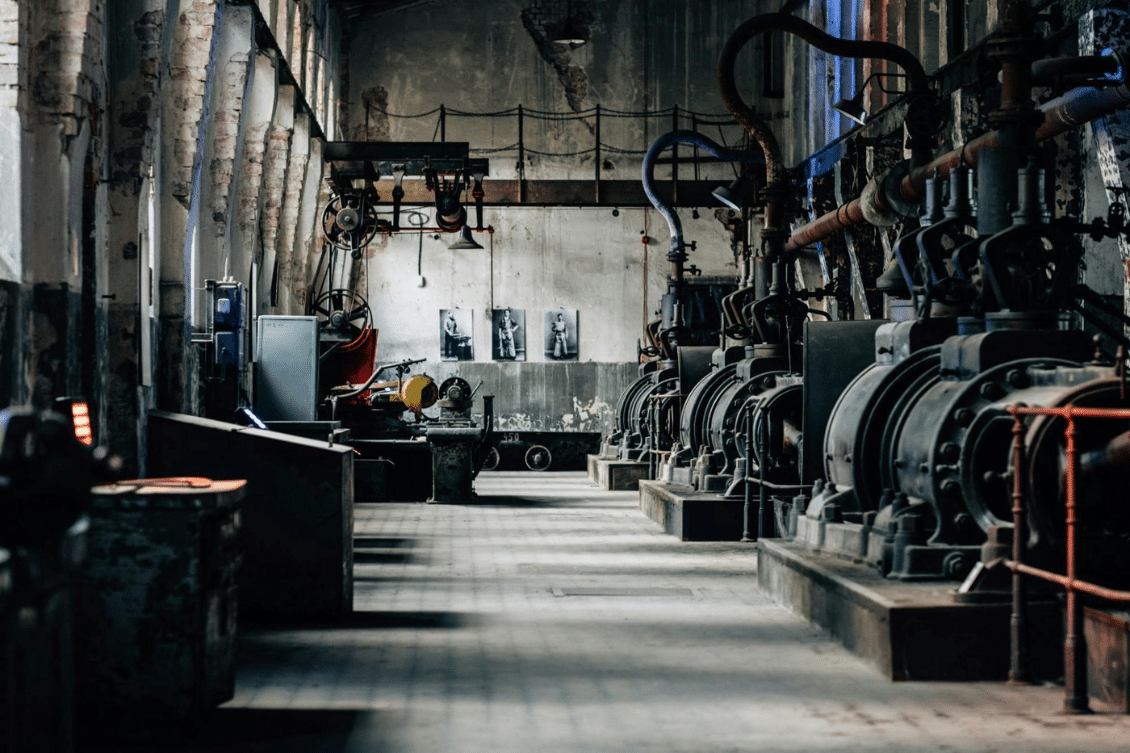
For the last few decades, China has become the manufacturing hub of the world. With its large production facilities, skilled workforce, and efficient supply chain it has become the primary destination for manufacturers of all sizes.
In recent years, there has been a noticeable shift and manufacturers are starting to expand outside of China. The reasons depend on the product you make, the industry you are in, and the size of your company but the start of a migration out of China has clearly begun. While China still remains the world’s production floor, manufacturers see a number of reasons and motivations to outsource products to another Asian country or to re-shore or near-shore.
In this blog, we will go over the five significant reasons manufacturers are migrating away from China. By examining these reasons, we can understand better the trends in the industry and learn more about the motivations of manufacturers of all different sizes.
Raising Costs in China
One of the main reasons why China was so attractive decades ago was its low production costs. For the last few years, the price of labor and overhead have gone up and therefore, the cost of doing business in China has increased as well.
However, is the price increase worth it?
Decades ago when China was the cheapest, they had big quality problems. However, manufacturers were willing to sacrifice quality for a very low-priced product. As China has improved its quality, its labor and overhead costs have also increased. The risk of manufacturers trying to move production out of China and into another low-wage country is that the quality of the product drops as well as the price.
Labor Costs Rising
As China’s economy has grown, the wages for employees in the manufacturing sector have also increased. In addition, with the economy growing, the workforce has become more skilled which has caused labor shortages. While the demand for labor is still high, it has caused wage rates to increase for labor, especially if the production facility is not easily accessible, such as not being by a train station.
Rising Overhead Costs
Wage rates are not the only thing increasing in China. You also have the majority of your operational expenses increasing, such as real estate. China’s urbanization wave has led to increased competition for land and resources, driving up property value.
Trade Tensions and Tariffs
The escalation of trade tensions between China and other countries, most notably the United States, has significantly reshaped the supply chain network. The imposition of tariffs and the emergence of trade disputes between major trading partners have had profound implications for manufacturers, disrupting supply chains and increasing costs across industries.
The trade tensions between China and the United States, characterized by tit-for-tat tariffs and retaliatory measures, have created uncertainty and volatility in global markets. Stemming from concerns over trade imbalances, intellectual property rights, and market access, these tensions have led to a period of economic uncertainty.
As low production costs were a reason to draw attention, China’s infrastructure and supply chain were another reason to keep manufacturers. Their supply chain has become interconnected and interdependent in today’s hyper-globalized economy. As tariffs are levied on goods imported from China and other affected regions, manufacturers face the challenge of navigating complex trade regulations, sourcing alternative suppliers, and restructuring production networks to mitigate the impact of tariff-induced cost increases.
Diversification of Supply Chain
Tariffs, viruses, and transportation costs have highlighted the importance of a diversified supply chain. The goal of a diversified supply chain is to reduce dependency on any single region or supplier and to build more agile and adaptable supply chain networks capable of responding to disruptions and uncertainties.
Diversifying supply chains involves spreading production facilities, sourcing activities, and distribution channels across multiple geographic locations, thereby reducing the vulnerability of businesses to localized disruptions and systemic risks. In short, you are setting up a separate supply chain not linked to your existing supply chain. This takes a lot of time but as history has shown us, it’s worth setting this up.
Against the backdrop of rising costs, trade tensions, and geopolitical uncertainties, manufacturers are increasingly exploring alternative production locations outside of China to reduce dependency on the world’s largest manufacturing hub. Countries in Southeast Asia, such as Vietnam, Thailand, and Malaysia, as well as emerging manufacturing hubs in Latin America, Eastern Europe, and Africa, are emerging as attractive destinations for companies seeking to diversify their production footprint and mitigate exposure to risks associated with concentrated supply chains.
These alternative production locations offer several advantages, including lower labor costs, competitive tax incentives, favorable regulatory environments, and proximity to key markets. Moreover, many of these countries have invested in infrastructure development, skills training, and technology adoption to attract foreign investment and foster industrial growth, further enhancing their appeal as manufacturing destinations.
Favorable Business Environments Elsewhere
As manufacturers seek alternatives to China for their production needs, other countries have emerged as compelling destinations offering favorable business environments conducive to manufacturing investment and growth. These nations boast a combination of strategic advantages, including supportive government policies, attractive incentives, and streamlined regulations, making them increasingly attractive to businesses looking to diversify their production footprint and mitigate risks associated with concentrated supply chains.
In addition to their strategic advantages, these countries also offer a range of incentives, tax breaks, and streamlined regulations designed to attract and support manufacturing investment:
By leveraging these incentives and favorable regulatory environments, manufacturers can capitalize on the opportunities presented by these dynamic markets, enhance operational efficiency, and position themselves for sustainable growth and competitiveness in the global marketplace. As businesses continue to navigate evolving market dynamics and seek to diversify their production strategies, countries offering favorable business environments are poised to attract a greater share of manufacturing investment and contribute to economic development and industrial expansion on a regional and global scale.
Advancements in Infrastructure and Technology
In emerging manufacturing countries, significant investments in infrastructure development and technological innovation have transformed these regions into attractive destinations for businesses seeking to expand their production capabilities and enhance competitiveness in the global marketplace.
Governments and private stakeholders in these countries have prioritized infrastructure development to support the needs of a growing manufacturing sector and facilitate economic growth. Investments in transportation networks, logistics infrastructure, energy systems, and telecommunications have laid the foundation for efficient and interconnected supply chains, enabling businesses to move goods and services more effectively across borders and access new markets.
In addition to infrastructure development, technological advancements play a pivotal role in driving efficiency, productivity, and innovation in manufacturing operations. Emerging manufacturing hubs are leveraging technology to optimize production processes, enhance product quality, and respond to evolving market demands.
Advanced manufacturing technologies such as automation, robotics, artificial intelligence, and data analytics are transforming traditional manufacturing practices, enabling businesses to streamline operations, reduce costs, and increase output. Automation and robotics, for instance, are revolutionizing production lines by automating repetitive tasks, improving precision, and increasing throughput, thereby enhancing overall efficiency and competitiveness.
Conclusion
The global manufacturing landscape is undergoing a huge transformation, marked by the shifting dynamics of production and supply chain management. From rising costs and trade tensions to the imperative for supply chain diversification and the emergence of new manufacturing hubs, the motivations driving this strategic realignment are multifaceted and far-reaching.
Countries such as Thailand, Vietnam, and Mexico are at the forefront of this transformative wave, offering favorable business environments, robust infrastructure, and technological innovation to support the needs of a dynamic and competitive manufacturing sector. By investing in infrastructure development, embracing digitalization, and implementing policies to attract foreign investment, these nations are positioning themselves as attractive destinations for businesses seeking to optimize production processes, enhance operational efficiency, and capitalize on emerging market opportunities.
By embracing the opportunities presented by emerging markets, technological advancements, and evolving consumer preferences, manufacturers can chart a course toward sustainable growth, resilience, and prosperity in the years to come.
By: Jared Haw
Join our newsletter to receive a weekly portion of news, articles, and tips about OpenBOM and our community.