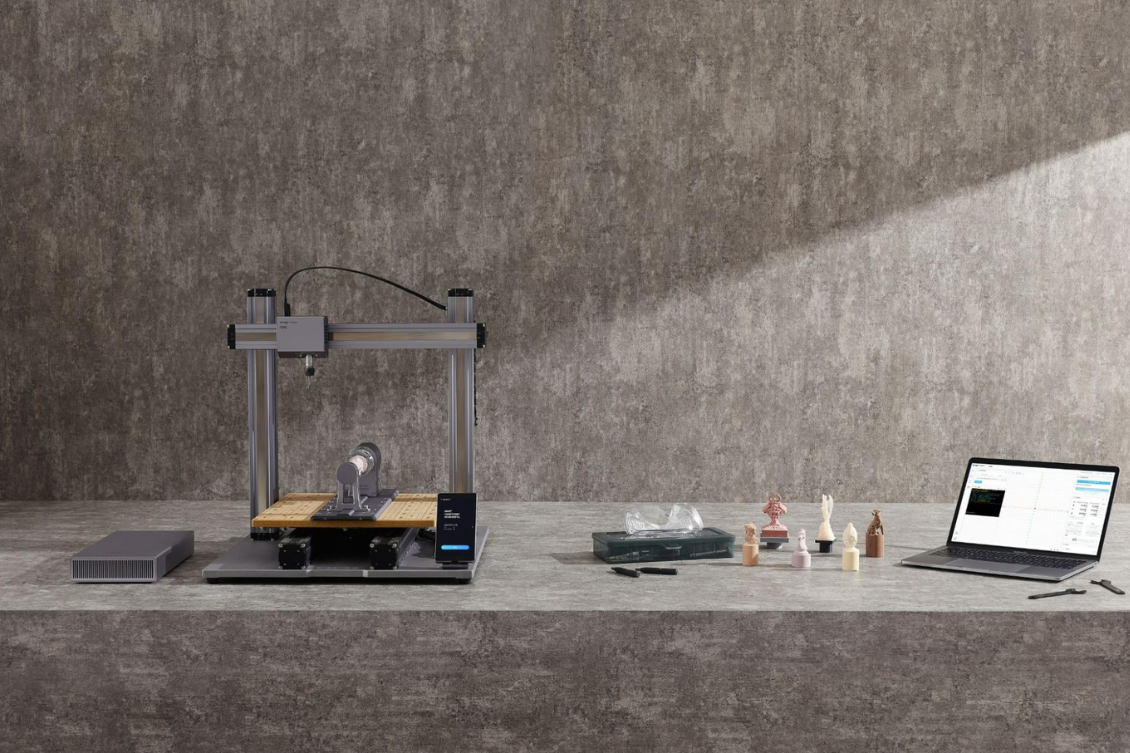
Managing the details of every part, component, and material involved in product development is both a challenge and a necessity. As a product moves through concept, prototype, and eventually to production, it requires constant updates and collaboration across multiple teams, from engineering and design to procurement and manufacturing. Relying on traditional tools like Excel or static documents to manage these details often leads to miscommunication, version control issues, and costly errors.
This is where a digital Bill of Materials (BOM) comes into play. A digital BOM is more than just a list; it’s a dynamic, real-time, centralized record that keeps every team member on the same page. By offering updated information on components, suppliers, quantities, and specifications, a digital BOM becomes the single source of truth throughout the product development process.
In this blog, we will explore three key reasons why managing a digital BOM is crucial to keeping development on track and achieving a successful launch.
Why You Need a Digital BOM During Product Development
Managing a product’s lifecycle from concept to production involves countless details and requires seamless communication across teams. Traditional BOMs, often created in Excel, lack the flexibility and accessibility needed to keep pace with today’s iterative and collaborative development processes. A digital BOM, by contrast, provides a single, up-to-date source of truth that all teams can access in real-time. This centralized, dynamic approach not only streamlines communication but also allows teams to stay agile, make fast decisions, and avoid costly mistakes. Here are three reasons why a digital BOM is essential for effective product development.
Improved Collaboration Across Teams
Effective product development hinges on collaboration between various teams, including engineering, design, procurement, and manufacturing. Each department plays a unique role in the process, and they must work in tandem to bring a product from concept to reality. However, traditional BOMs can create silos of information. When one team updates a part or component, other teams may not receive that information in a timely manner, leading to miscommunication, duplicated efforts, or, worse, the use of outdated data.
A digital BOM addresses these challenges by providing a real-time, centralized source of information that is accessible to all stakeholders involved in product development. This transparency creates a collaborative environment where teams can easily share insights and updates. For example, when engineers make a design change, the changes are immediately reflected in the digital BOM. Procurement teams can quickly access the most current specifications and quantities, ensuring that prototype orders are placed for the correct parts. This seamless flow of information reduces the risk of errors and helps teams respond more effectively to changes, ultimately improving the overall efficiency of the development process.
Moreover, a digital BOM facilitates better communication among teams by streamlining discussions and reducing the need for lengthy email chains or meetings to clarify information. With everyone working from the same updated BOM, teams can focus on their specific tasks without worrying about whether they have the latest data. This collaborative approach not only enhances productivity but also builds stronger relationships between departments, as each team becomes more aware of the others’ needs and contributions. Ultimately, by improving collaboration through a digital BOM, companies can accelerate the product development cycle and bring innovative products to market more effectively.
Enhanced Flexibility and Faster Iteration Cycles
In the dynamic landscape of product development, the ability to adapt quickly to changes is crucial for success. Design modifications, feedback from testing, and new market requirements can arise at any time, necessitating swift adjustments. Excel BOMs, often struggle to keep up with these rapid changes. When teams are forced to make manual updates, they risk introducing errors and inconsistencies, which can slow down the entire development process.
A digital BOM, on the other hand, offers the flexibility needed to accommodate frequent iterations seamlessly. It allows teams to make real-time updates without disrupting workflows. For instance, when engineers need to revise a part specification based on testing results, they can quickly modify the digital BOM to reflect those changes. This immediate visibility enables procurement teams to order the correct components right away, reducing lead times and ensuring that production schedules remain on track. The agility provided by a digital BOM facilitates faster iteration cycles, allowing companies to respond to feedback and pivot when necessary.
Moreover, the enhanced flexibility of a digital BOM supports a more iterative design process, where teams can experiment and innovate without the fear of losing track of previous versions or changes. As modifications are made, the digital BOM maintains a clear history of revisions, providing visibility into how the product has evolved over time. This capability not only encourages creativity but also helps teams assess the impact of each change, ultimately leading to better decision-making and a more refined final product. By enabling faster iterations and supporting agile development practices, a digital BOM empowers teams to bring high-quality products to market more efficiently.
Reduced Risk of Errors and Miscommunication
One of the most significant challenges in product development is the potential for errors and miscommunication, which can arise from relying on outdated or fragmented information. When teams use traditional BOMs, such as Excel spreadsheets, the risk of mistakes increases due to version control issues, human error during data entry, and the lack of real-time updates. A single incorrect part number or miscommunication about specifications can lead to costly production delays, increased expenses, and even damage to a company’s reputation.
A digital BOM significantly mitigates these risks by serving as a centralized and real-time repository of information. With all stakeholders accessing the same up-to-date data, the chances of errors occurring decrease substantially. For example, if a design change is made, it is immediately reflected in the digital BOM, ensuring that all teams, engineering, procurement, and manufacturing, are working from the same accurate information. This synchronization minimizes the likelihood of using outdated or incorrect data, which can lead to incorrect orders, manufacturing delays, or rework.
Additionally, a digital BOM often includes features that enhance communication, such as comments, notifications, and change tracking. These tools facilitate transparent dialogue among team members, making it easier to clarify questions and address concerns as they arise. For instance, if a procurement team has a question about a component, they can leave a note within the digital BOM, allowing engineers to respond promptly. This immediate feedback loop not only reduces misunderstandings but also fosters a culture of collaboration, where teams feel empowered to communicate openly and address issues as they arise.
Ultimately, by reducing the risk of errors and miscommunication, a digital BOM contributes to a smoother product development process. This increased accuracy and clarity not only saves time and resources but also enhances the overall quality of the final product, ensuring that it meets both company standards and customer expectations.
Conclusion
Effective product development requires precise coordination, flexibility, and clear communication among diverse teams. A digital BOM is essential for navigating these challenges, offering a centralized platform that enhances collaboration, supports rapid iterations, and minimizes the risk of errors. By adopting a digital BOM, organizations can streamline their development processes, respond swiftly to changes, and ensure that every team is aligned with the latest information.
As you bring your products to market efficiently and effectively, consider the impact a digital BOM can have on your development efforts. Embracing this technology not only improves internal workflows but also positions your company for success in an ever-evolving marketplace. Investing in a digital BOM is not just a step forward in managing product data; it is a commitment to innovation, quality, and excellence in every aspect of your product development journey.
By: Jared Haw
Join our newsletter to receive a weekly portion of news, articles, and tips about OpenBOM and our community.