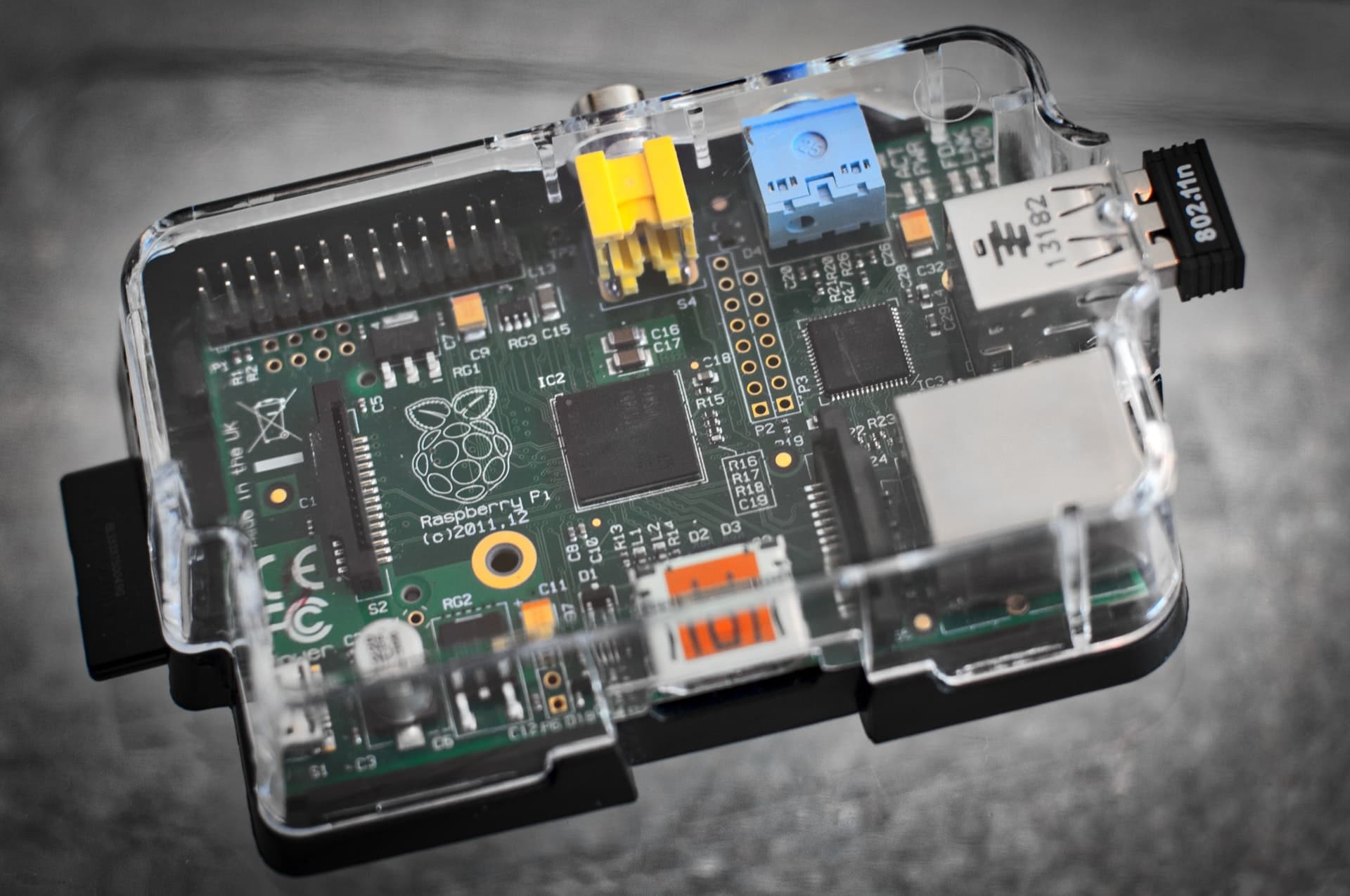
One very common question is, “after this prototype, can we go straight into mass production?” And when they hear, not really, they will ask, “why not? If we can create a prototype, why can’t we replicate that in mass production?”
Being able to go straight into production from prototypes is a common misconception, and unfortunately, life is not that simple.
Why You Cannot Replicate The Prototype?
The most important question you need to ask yourself before going into mass production is how can we replicate the sample we have so we can go into mass production. And usually, you can not quickly and cost-effectively replicate prototypes at high volume. So, there are some things you need to work out before production.
The prototypes you have can not be replicated for a number of reasons, such as:
- You can’t scale the prototype processes (such as 3D printing).
- You can cost-effectively scale 3D printing processes. The cost to CNC rather than die-cast is significantly higher (same with 3D printing & plastic injection molding).
- You can’t take a design of a prototype part (assuming it’s 3D printed or CNC) and open a tool for it right away. You need to design that part for tooling, this is called design for manufacturing (DFM).
- Can’t replicate without a transfer of knowledge. Usually, during prototypes, the engineer handcrafting it. The operators on the line lack the knowledge of how to assemble the product at first.
What Are the Risks of Moving Fast?
However, if you still decide for some reason to go from prototypes to mass production then you can expect the following results:
- Longer lead times. Ironically, usually, companies want to cut out any middle steps because they believe they can ship faster. That’s rarely the case.
- Increased production costs. The parts are not optimized for production so you need to pay more for them.
- Increased scrap rate. It’s common to expect a 3% defect rate but failing to go through the correct processes can see a much higher defect rate, such as 50%+
I think it’s clear that there are steps needed in-between prototypes and mass production. But what are they? But first, what is the goal of production?
The goal of mass production is to produce a consistent product at the lowest possible cost, while at a high quality again and again.
The question you need to answer is, how to create a product you can replicate over and over again that is high quality and can be produced cost-effectively?
Before Mass Production Checklist
Here is a shortlist of tasks that need to be accomplished after prototypes and before mass production. These differ within industries but these are the building blocks.
- Tooling, jigs, and fixtures: The point of creating tools, jigs, and fixtures is that they create consistency during the production process.
- Part Optimization: This usually consists of DFM and engineering the parts for tooling, so the parts can be replicated in production and assembly.
- Production Work Instructions (WIs) or Standard Operating Procedures (SOPs): Details the steps to fabricate each part and assemble each product.
- Quality Documents. You need objective standards of what is acceptable and what is not acceptable.
- The Pilot Run: The pilot run is a small percent of the first production run that is done to ensure that all of the tools, processes, and labor come together. If there is a large defect rate during the pilot run then you can quickly stop and diagnose the problem(s).
To go smoothly into production, it’s important to take these steps. Failing to take these extra steps and following the correct process will put your product launch at risk.
What Can You Do Today?
When you are launching your product, there will be multiple revisions and change requests that must be managed. It is easy to lose historical data or fail to share changes with the correct team members. A centralized platform that connects your team, contractors, and suppliers is your solution.
OpenBOM is a cloud-based platform to manage your engineering and manufacturing data. Companies from startups to Fortune 500’s use OpenBOM to create a centralized database to bring in, store and manage their manufacturing data. With this infrastructure, users also use OpenBOM to streamline both their change management and PO processes.
If you need to improve the way you manage your data and processes, contact us today for a free consultation.
Regards,
Jared Haw
Join our newsletter to receive a weekly portion of news, articles, and tips about OpenBOM and our community.