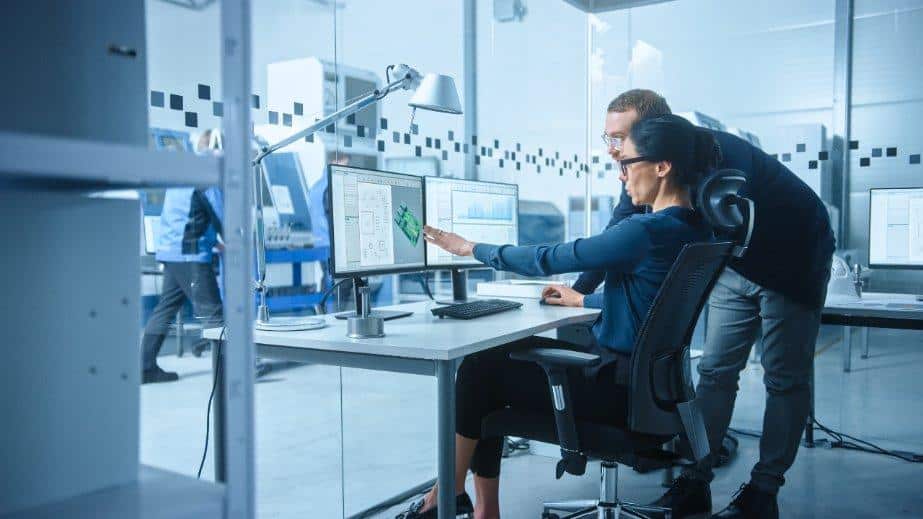
A very common question every manufacturing company needs to answer is when to start working with their contract manufacturer (CM). While initiating contact earlier is always better, getting your CM involved early can end up hurting your company.
During the NPI steps, multiple steps should be followed to transition into production smoothly. If these steps are not followed, you risk having a failed launch or a delayed launch.
While it can always be wise to integrate your CM earlier for things like quotations and prototypes. Handing off the entire product to your CM too soon can be counter-productive.
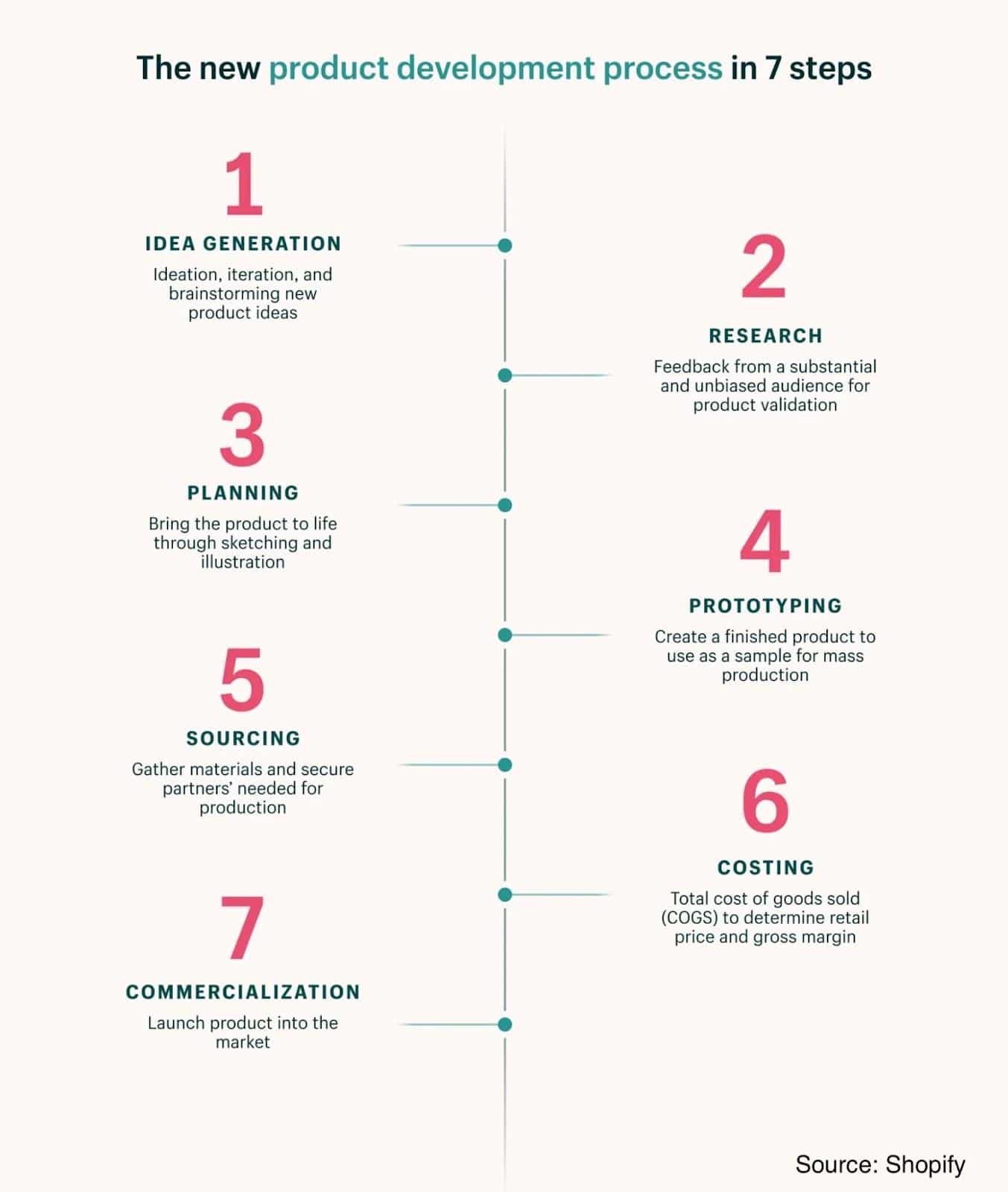
If you are in the following stages then it’s too early to involve your CM:
You are at the concept stage
If you are at the concept stage then congrats. It can be a fun stage with a lot of brainstorming. However, there is no seat at the table for a CM. While a CM does have multiple strengths, brainstorming ideas for a new client is not one of them.
This can work in some industries with short development cycles and if the CM is a parent company of a brand. However, for the majority of the cases, do not bring your CM to the concept stage.
You are Pre Prototype
If you have not made a prototype then you are most likely too early to work with a CM. One purpose of making a prototype is to share it with your target market to receive feedback. If you do not have this feedback then you are not sure if there is a demand for your product. Without knowing if there is demand for your product then is it necessary to talk to the company who will make it in production?
However, once you do have a prototype and you need to make some refinements, then it’s a good time to discuss these steps with your CM.
You are at the Industrial Design Stage
The industrial design phase is an exciting stage. You see what the product can look like. It will not be functional but you will have some renderings of what it can look like. Usually, the person who is designing this should have an understanding of the industry and of the market.
At this stage of development, the CM is unable to provide any support.
No Clear Business Plan
Expecting customers to find you is not a business plan. You need to develop a sales plan, funding plan, marketing plan, go-to-market plan, and more. If you do not have these then no one will buy your product. If no one will buy your product then is it necessary to have someone make it.
You first need to build demand for your product. After you build demand, you can find someone to make it.
What Would Happen if I go to a CM too Early?
While I always suggest contacting your CM and building a relationship with them as a positive thing, working with them too early can be counter-productive. The strength of your CM is to build your product. This usually starts with a request for quotation (RFQ), leads into design for manufacturing (DFM), and then can lead to prototypes with multiple design revisions, and always ends with mass production. Using them for other activities will not provide you with a lot of value.
Here are the results of working with your CM too early:
- The supplier’s goal (just like yours) is to make money. If they are working with a client that is taking too long then they will get annoyed and stop working with you.
- They might make certain revisions that are not up to your requirements or will fail during the certification process.
- If you go into production and can’t sell it then someone will be forced to hold that inventory. If you force the CM to hold it then expect extra charges, increased prices, and refusal to accept future POs.
- Everything will take longer. CMs put assets where money is made. This means they put people in areas of the business that makes money. This means your project will sink to the bottom of the priority list and things will take longer.
I am ready. What do I do now?
If you are following the steps and have a prototype, a business plan, and the correct product data then it’s probably a good time for you to start working with your CM. The most important step to building a foundation is to create a centralized platform that connects yourself and your supplier(s).
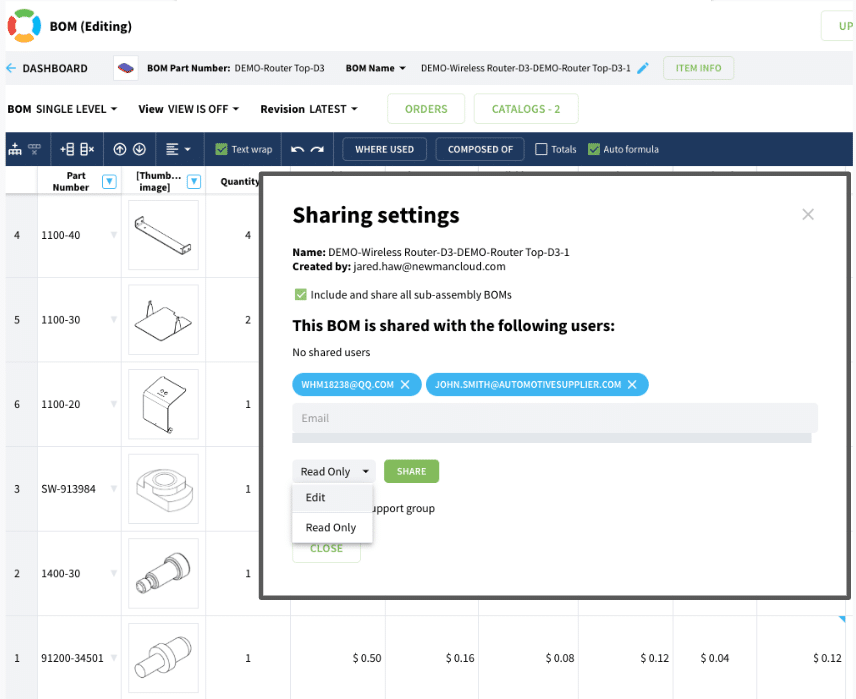
With this platform, you can automatically share data and keep everyone updated with the most up-to-date data. The worst thing is to have your CM create unapproved changes, forget which version you are working on, or not have a clear understanding of costs. OpenBOM eliminates these problems.
OpenBOM is a cloud-based platform to manage your engineering and manufacturing data. Companies from startups to Fortune 500’s use OpenBOM to create a centralized database to bring in, store and manage their manufacturing data. With this infrastructure, users also use OpenBOM to streamline both their change management and PO processes.
If you need to improve the way you manage your data and processes, contact us today for a free consultation.
Regards,
Jared Haw
Join our newsletter to receive a weekly portion of news, articles, and tips about OpenBOM and our community.