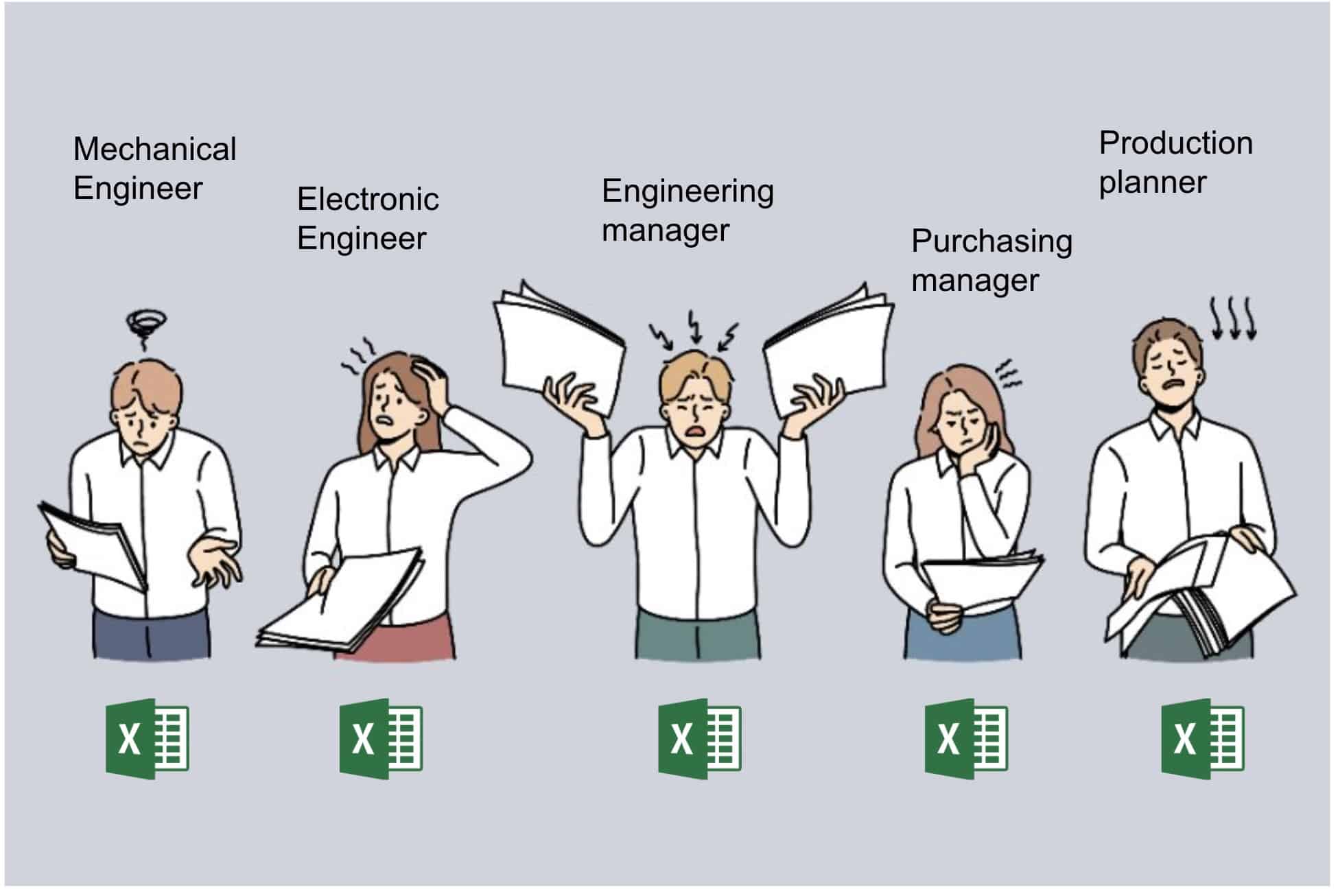
Most successful digital transformations include a component of improved data and process management solutions. Manufacturing organizations that digitize their operations increase their efficiency and optimize their workflows. However, even the best-laid plans can be hobbled by a bad data foundation – poor BOM management. This article discusses why bad BOM management can slow down your digital transformation efforts and offers some tips for getting your BOM under control.
As the manufacturing sector undergoes a digital transformation, many organizations are finding that poor data organization about products, including all bill of materials (BOM) and data that are dependent on it is holding them back. A well-organized and accurate BOM is an essential organization downstream processes such as production planning, and procurement and also a critical element in cost estimation, contract manufacturing, and others. However, unfortunately, many companies struggle with this critical task. In this article, we’ll explore some of the reasons why bad BOM management can hurt your transformation efforts, as well as offer some tips for improving your organization’s BOM practices.
Why do engineers say – I’m ok with Excel?
I asked engineers in the SOLIDWORKS user group how they manage BOMs and got astonishing results of more than 70% saying – I’m good with Excel. A large number of engineers using SOLIDWORKS are still emailing BOM Excels and sharing files via email. While at first glance you can think about it as “no problem”, things are great. After talking to some of them, I found a lot of details, very interesting reactions, problems, and challenges.
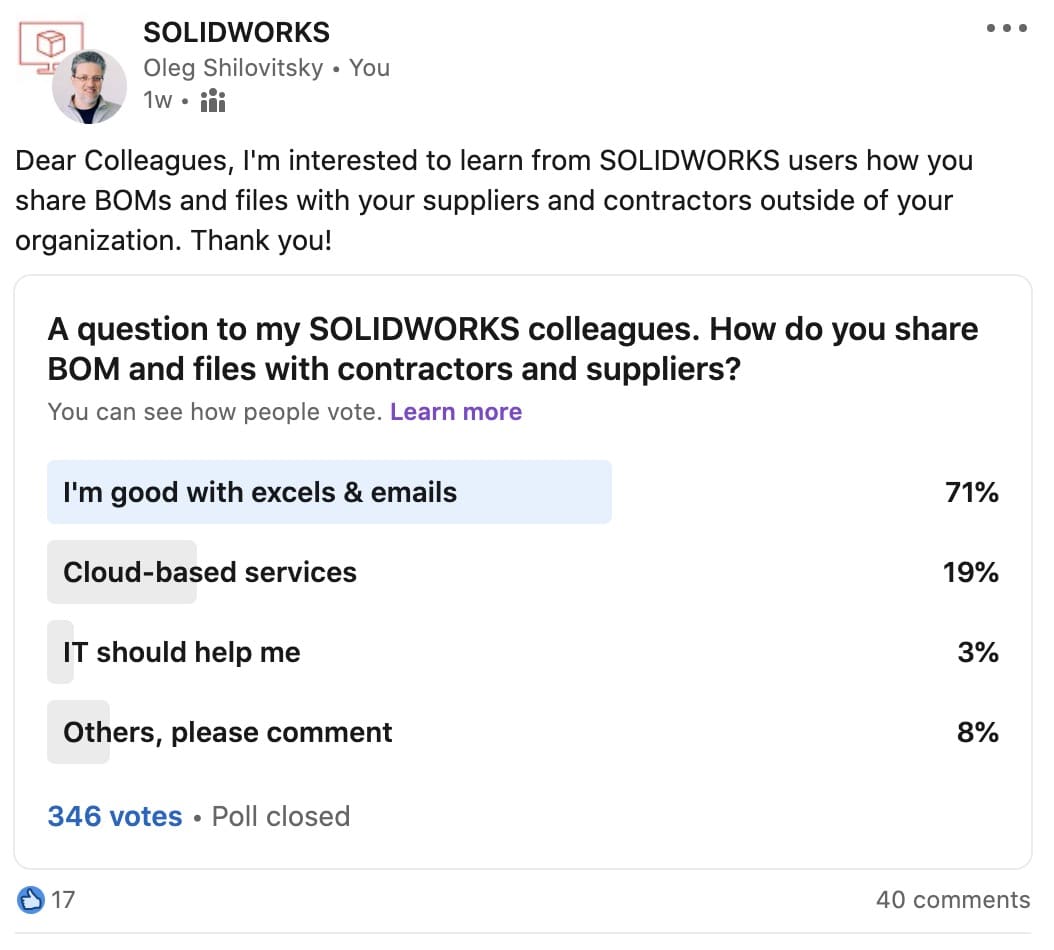
Talking to many of these engineers helped me to understand their answers better. Engineers are not responsible for data management strategy and are not supposed to deal with laying down the foundation of the digital process. Engineers by nature are “problem solvers”. They are looking for an easy way (for them) to kick off the process of planning and they do it by exporting information to a spreadsheet. The problems are coming later and include many challenges and damages to business outcomes. Teams are not staying on the same page managing BOM structure using Excel. The data is lost and the engineering bill is disconnected from the manufacturing bill of materials, not providing information for supply chain efforts and procurement.
Changes Are Hard
While most of the engineers and other people in manufacturing companies understand the problems BOM management in Excel brings, not many of them are ready to stand against existing poor data management practices. After all, even the worst possible solution is still part of everyday habits, and making a change is hard. Here are four reasons that slow down companies from ditching Excel.
- The complexity of data management
- Legacy tools
- High cost of solutions
- Absence of data management strategy
Even the smallest company or engineering team lives in silos. Everyone is focusing on how to solve their individual problems and the biggest problem is to establish a data management strategy to manage information flows.
How to Switch To Digital BOM?
One of my favorite quotes by Lao Tzu says “A journey of a thousand miles must begin with the first step.” In the same way, manufacturing teams can start their digital transformation journey by laying down a foundation of digital BOM, which will change the way data is managed and delivered to all team members involved in the design, planning, production, sales, and maintenance processes. Here are three elements of the switch:
- Use “one-click BOM” provided by OpenBOM CAD Add-ins to automatically capture all the information needed from the design including product structure, geometrical information, CAD files, and derivative files (eg. PDF, STEP, DXF, etc.)
- Use flexible data modeling tools provided by OpenBOM to create all elements of business data to support product development and downstream processes. It includes but is not limited to cost information, manufacturers and suppliers, contract manufacturing activities, and many others.
- Define role-based access and mechanisms to identify what data should be available to whom in the company and to contractors and suppliers. OpenBOM team views is the mechanism that can help to support instant real-time data sharing. If everyone is not ready to make a switch, OpenBOM’s out-of-the-box flexible export functions can instantly create an Excel (or zip file) with all information needed.
Conclusion
Manufacturing companies should lay down a healthy data foundation for their digital transformation efforts. One of the most important elements of this data foundation is a digital BOM. Such an element of data foundation creates digital records for your product which is an essential part of digital product development. Relying on Excel, spreadsheets, and drawing tables can give you an illusion that “work is done”, but eventually will lead to mistakes, additional costs, and delays. However, the change is hard and engineers alone cannot make it happen. Digital technologies are available now, but companies need to develop a digital transformation strategy that will help them to create a roadmap of how the entire company will migrate their business processes from old and clunky Excels to better tools and business processes.
OpenBOM provides a digital technology to manage data and to support team collaboration to manage product data, engineering, and manufacturing BOM, which includes all elements of the product and services. It goes beyond the information included in each CAD BOM (MCAD, PCB, etc.) and allows to build a comprehensive structured information set with the foundation of engineering BOM that can be used in other product development disciplines such as supply chain management, production order & work instructions, cost estimation and connected enterprise disciplines.
REGISTER FOR FREE to check how OpenBOM can help.
Best, Oleg
Join our newsletter to receive a weekly portion of news, articles, and tips about OpenBOM and our community.