What is it?
Product cost management helps companies estimate the costs of their products, systems or solutions over their lifecycles.
It provides visibility into the cost associated with your product and supply chain while allowing you to track and maintain costs at a granular level of detail to meet your product and market specifications.
Product cost management is a complex problem that requires a collaborative effort to manage and may require complex data allocation.
Effective product cost management manages a product’s lifecycle cost against a company’s target cost objectives and maximizes lifecycle profitability.
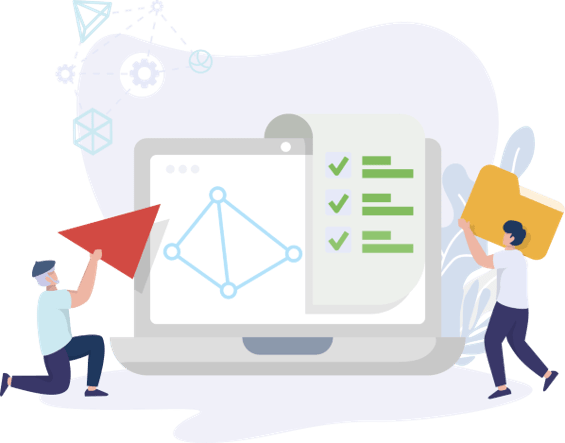
Why do you need it?
Product cost management provides transparency into cost drivers, enabling companies to identify cost outliers and trends by assessing costs at a detailed level.
It allows key people within sales/marketing, procurement, operations, and engineering to collaborate on product design decisions.
Your teams can reduce product costs by identifying and leveraging opportunities across suppliers and manufacturing partners.
By estimating, tracking, and controlling costs throughout the product lifecycle, companies can maximize product profit margins and return on investment.
Why is OpenBOM different?
With OpenBOM, you can store, organize, and manage your products, items, cost properties, and formulas with ease. With OpenBOM you can collect data from multiple items, choose your preferred suppliers, and calculate costs based on the product structure.
The core of OpenBOM is a global, multi-tenant, flexible information model. It provides an easy way to organize products and track your costs, with cost information and models for rollups and calculations.
OpenBOM provides flexible formula and calculation support mechanisms. Using OpenBOM’s formulas you can easily roll up costs and perform operations on any data properties stored in OpenBOM.
OpenBOM reduces manual cost maintenance tasks by providing automated cost calculations and rollups.
How does it work?
OpenBOM allows you to efficiently manage your product costing.
First, you need to create a catalog with your items. This can be done manually or through the import of your items from a spreadsheet or your favorite CAD software. Once you have imported your items, you simply need to add the cost for each item. These costs can be saved in the catalog for future use. This may have already been done if the costs were included in your imported information.
You can add a formula to calculate costs and perform rollups. Formulas are equations you create in a cell which perform simple arithmetic operations for you by using the designated cells. OpenBOM is able to collect data from multiple items, choose preferred suppliers, and calculate the cost based on the BOM. OpenBOM formulas and calculations are a powerful yet flexible mechanism to perform important calculations.
In a regular formula without sub-levels, formulas work in OpenBOM in a similar way to Excel. However, OpenBOM differs when sub-levels are involved. In this instance, we first compute the cost for each regular sub-level item using the regular formula. Then we sum it up for all the sub-level items and put it into the cost for the parent, and then apply the formula to the parent level.
Finally, you also have the option of defining purchased assemblies, which allows you to keep an entire BOM while skipping parts and components from assemblies that were already purchased for a specific price.
If you are interested in learning more about product cost management, click here and take a look at this blog post.