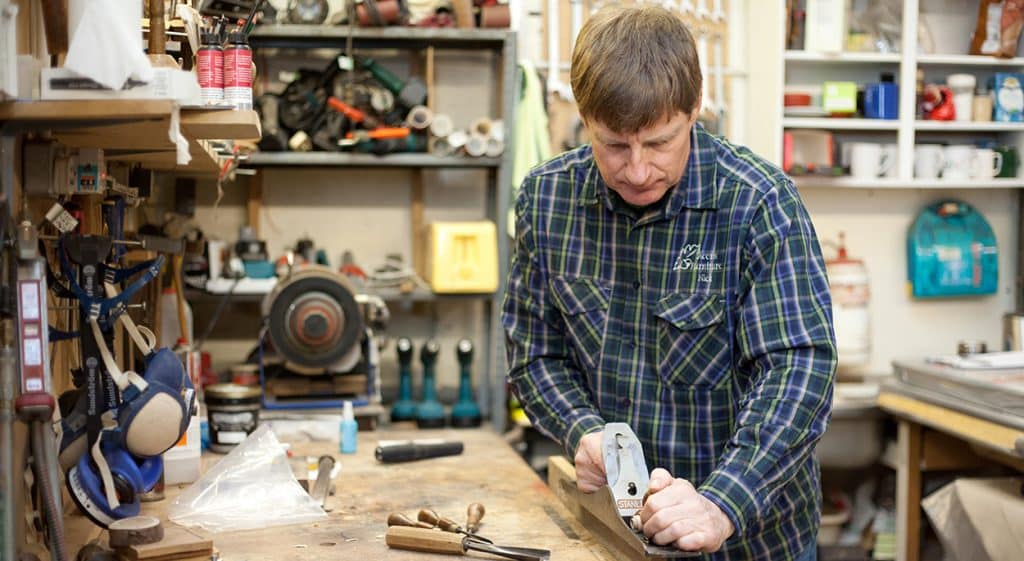
North Wales furniture maker Nick Lumb, who trades as Acorn Furniture, relies on OpenBOM to create accurate material cutting lists for his one-of-a-kind bespoke products.
Working primarily in British hardwoods and to specifications developed together with the customer, the design process in Onshape is key to the firm’s success on many fronts. Material planning and procurement are made more reliable and painless by OpenBOM’s cutting list feature which includes part length, width, and thickness.
“I need an accurate cutting list because I need to make parts”, says chemical engineer turned woodworker Nick Lumb. “While the concept is simple, the activity most certainly is not.”
“Oddly, a conventional bill of materials is not what I need”, says Nick, “I need an accurate list of material sizes by item which I will then cut from raw materials.”
Most of the timber Nick uses has been milled and dried on his premises from local Welsh hardwoods, sometimes from trees that Nick has felled himself, or even felled and milled the Customer’s own tree on their premises.
“For me, the OpenBOM cutting list is important because it includes all the information I need to select for that wood item in my workshop; material type, dimensions, length/width/thickness, it is something I can print and take to the shop with me and is accurately tied to the 3D design.”
Moreover, as Acorn’s products often contain mirrored items like legs or corner posts, the ability to combine them using OpenBOM’s ‘Combine by Name’ is also important to Nick. Once all timber parts have been cut from planks and planed all around, then drawings are referred to for joint details that are the mirrored features.
Nick does it all at Acorn, customer interviews, concepts & designs, makes the furniture, final assembly, and loading in the Land Rover for delivery to the customer.
Reflecting over the years, Nick has seen his share of digital design tools before finally settling on Onshape and OpenBOM to best serve his discerning clientele.
“OpenBOM is a fantastic extension to Onshape as it gives me an accurate, live, cutting list tied back one hundred percent to my model”.
Like any manufacturer of custom products, there are often last-minute changes leading up to the final design. Sometimes the customer asks for that last-minute change but more often, using locally sourced British timber, which has more ‘features’ than commercial timber, the design needs tweaking to make allowances.
“In the past, producing a cutting list manually without OpenBOM was tedious and error-prone, made even worse if you want to make some changes”
“With OpenBOM inside of Onshape, I literally make the change to the design, click Update BOM and by the time I have poured my tea, the new cutting list is ready.”
“It’s that easy.”
Nick likes the way OpenBOM and Onshape work well together.
According to Nick, “I appreciate the improvements both products continue to make. The benefit to me and my customers is well worth the investment.”
“OpenBOM works the way I work”.
For more information on Acorn Furniture please visit www.acorn-furniture.co.uk
For more information on OpenBOM please visit www.openbom.com
Join our newsletter to receive a weekly portion of news, articles, and tips about OpenBOM and our community.